Blue laser welding machine weld for copper 2~5mm reduce splashing and improve welding speed
Time:2023-11-14
Views:616
Blue laser welding machine
weld for copper 2~5mm reduce splashing and improve welding speed
weld for copper 2~5mm reduce splashing and improve welding speed
The development of industrial laser technology has always been along the roadmap of production technology and new social requirements. Over the past 60 years, laser technology has made significant contributions to solving important tasks for the future of humanity, from the digital economy and society to sustainable energy and healthy living. Today, from production technology to automotive engineering, medical technology, measurement and environmental technology, to information and communication technology, laser technology has become an indispensable part of many core areas of China‘s economy.
With the continuous progress of metal processing technology and the increasing demands of users, lasers need to innovate in terms of cost, energy efficiency, and laser system performance. The market demand for effective processing of highly reflective metals has stimulated the development of blue high-power laser technology and will definitely open the door to new metal processing technologies.
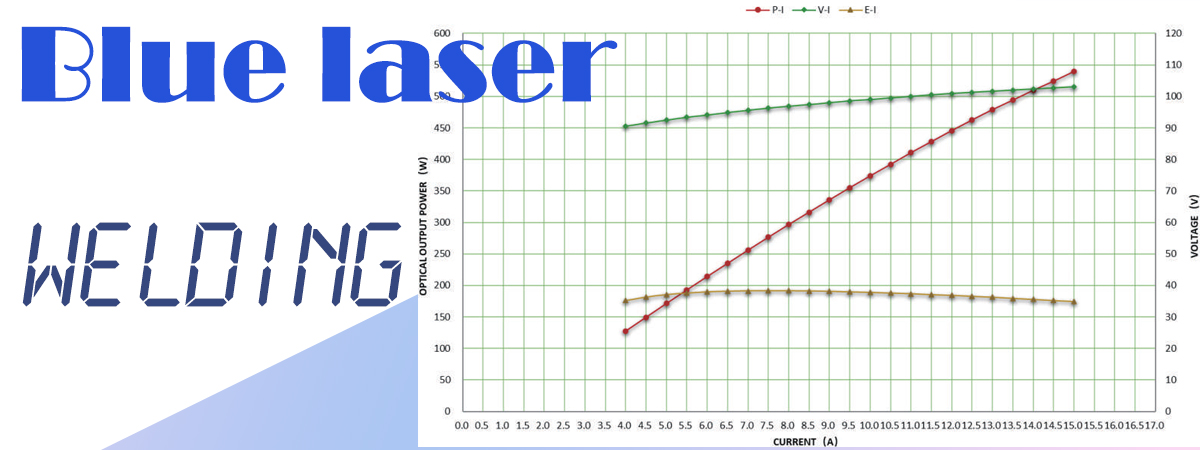
With the continuous progress of metal processing technology and the increasing demands of users, lasers need to innovate in terms of cost, energy efficiency, and laser system performance. The market demand for effective processing of highly reflective metals has stimulated the development of blue high-power laser technology and will definitely open the door to new metal processing technologies.
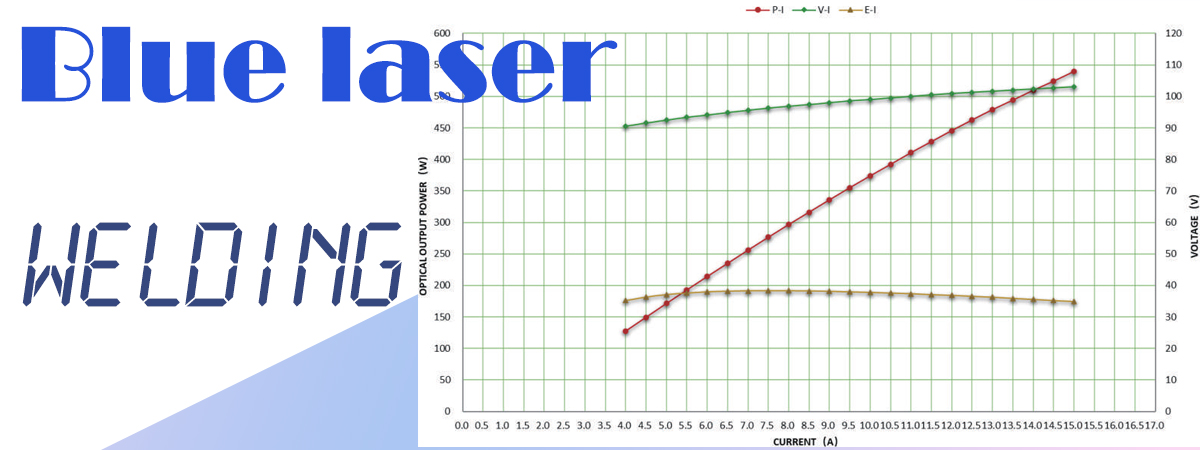
For non-ferrous metals, their absorption of light energy increases with the reduction of light wavelength. For example, copper‘s absorption of light at wavelengths below 500nm will increase by at least 50% compared to infrared light, making short wavelengths more suitable for copper processing. The problem is that developing short wavelength high-power lasers for these industrial applications is relatively difficult, with almost no high-power options available, and even existing options are expensive and inefficient. For example, there are some solid-state laser sources on the market based on frequency doubling that can be used within this wavelength range, producing lasers with wavelengths of 515nm and 532nm (green spectrum). However, these laser sources rely on their nonlinear optical crystals to convert pump laser energy into target wavelength energy, which results in high power loss. At the same time, lasers require complex cooling systems and optical settings.
In order to address this challenge, people have turned their attention to blue light semiconductor lasers. One reason is that blue light has its specific properties. High reflectivity metal materials have a high absorption rate for blue light, which means that blue light has a huge advantage in metal processing of high reflectivity materials such as copper. As shown in Figure 1, copper has a 13% higher absorption of blue light than infrared light × (13 times) or more.
In addition, the absorption rate of copper does not change significantly during melting. Once the blue laser starts welding, the same energy density will allow the welding to continue. Blue laser welding has inherent good control and minimal defects, resulting in fast and high-quality copper welds. Meanwhile, blue light absorbs less in seawater, resulting in a longer transmission distance, making it practical to explore the field of underwater laser material processing. In addition, blue light is relatively easy to convert into white light, so blue lasers can be used very compactly to achieve floodlights and other lighting applications. Secondly, semiconductor lasers based on gallium nitride materials can directly generate lasers with a wavelength of 450nm without the need for further frequency doubling, thus having higher energy conversion efficiency.
In addition, the absorption rate of copper does not change significantly during melting. Once the blue laser starts welding, the same energy density will allow the welding to continue. Blue laser welding has inherent good control and minimal defects, resulting in fast and high-quality copper welds. Meanwhile, blue light absorbs less in seawater, resulting in a longer transmission distance, making it practical to explore the field of underwater laser material processing. In addition, blue light is relatively easy to convert into white light, so blue lasers can be used very compactly to achieve floodlights and other lighting applications. Secondly, semiconductor lasers based on gallium nitride materials can directly generate lasers with a wavelength of 450nm without the need for further frequency doubling, thus having higher energy conversion efficiency.
The processing efficiency of copper materials using a laser with a wavelength of 450nm is expected to increase by nearly 20 times compared to a wavelength of 1 µ m. Compared with traditional near-infrared laser welding processes, high-power blue lasers have advantages in both quantity and quality.
Quantitative advantages: Improved welding speed, expanded process range, directly converted to faster production efficiency, and minimized production downtime. Quality advantage: It can obtain a larger process range, high-quality welds without splashes and pores, as well as higher mechanical strength and lower electrical resistivity. The consistency of welding quality can greatly improve the production yield (see Figure 2). In addition, blue laser can also perform thermal welding mode, which is impossible for near-infrared laser to achieve.
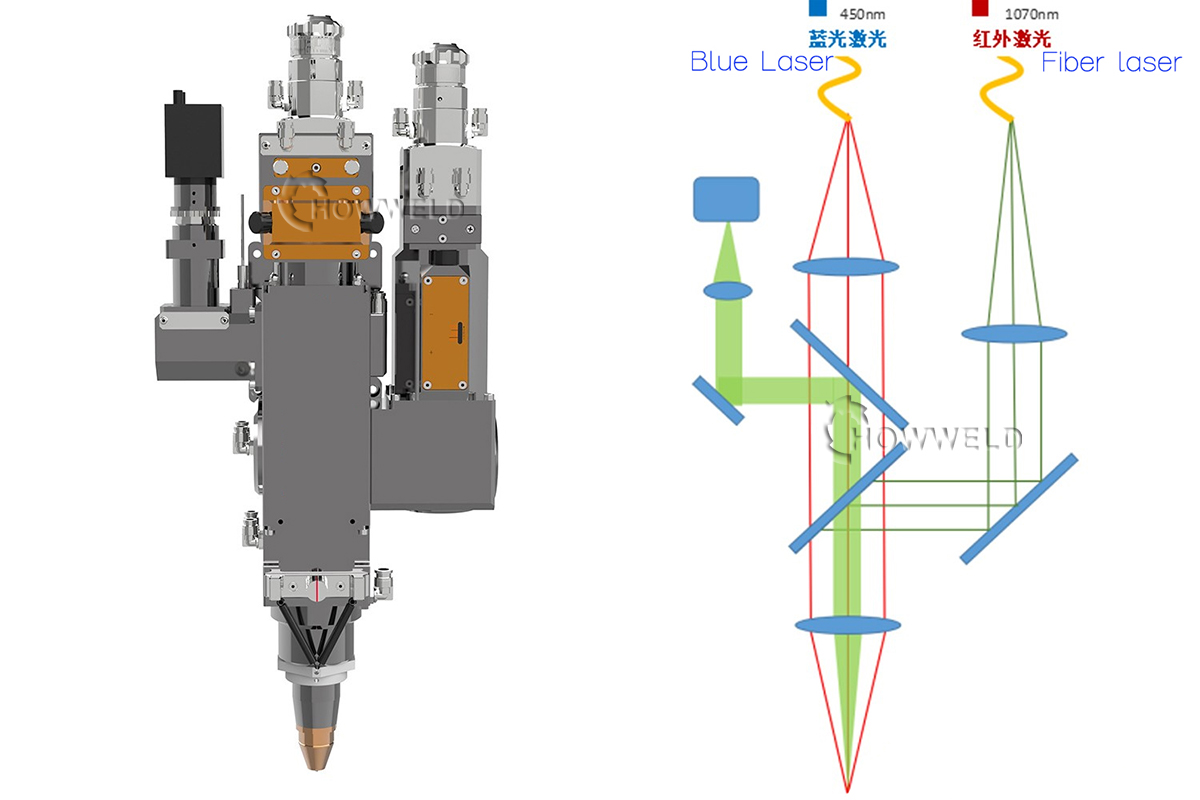
Quantitative advantages: Improved welding speed, expanded process range, directly converted to faster production efficiency, and minimized production downtime. Quality advantage: It can obtain a larger process range, high-quality welds without splashes and pores, as well as higher mechanical strength and lower electrical resistivity. The consistency of welding quality can greatly improve the production yield (see Figure 2). In addition, blue laser can also perform thermal welding mode, which is impossible for near-infrared laser to achieve.
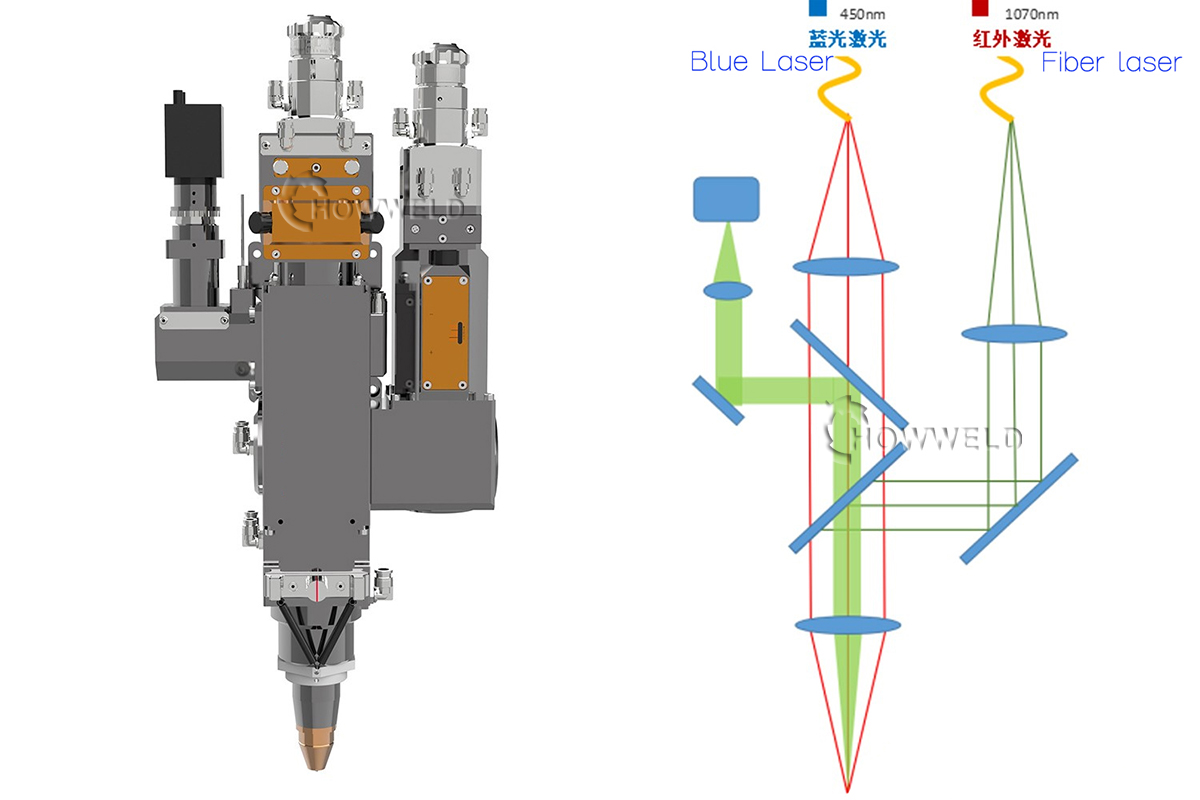
Machine was hybrid one:
One is blue is 1000w. Another is fiber laser 3000w Raycus.
Both laser connect into one welding head, do welding.
Weld for copper and aluminum.
Advance
1. Copper absorb blue laser, more than 40%.
Weld for copper, reduce splashing and improve welding speed
2. Price too high.
Shortcomings
Power density is still relatively low.
Low power leads to weak welding ability.
At present, it is mainly suitable for welding thin copper materials or copper foil below 1~1.5mm.
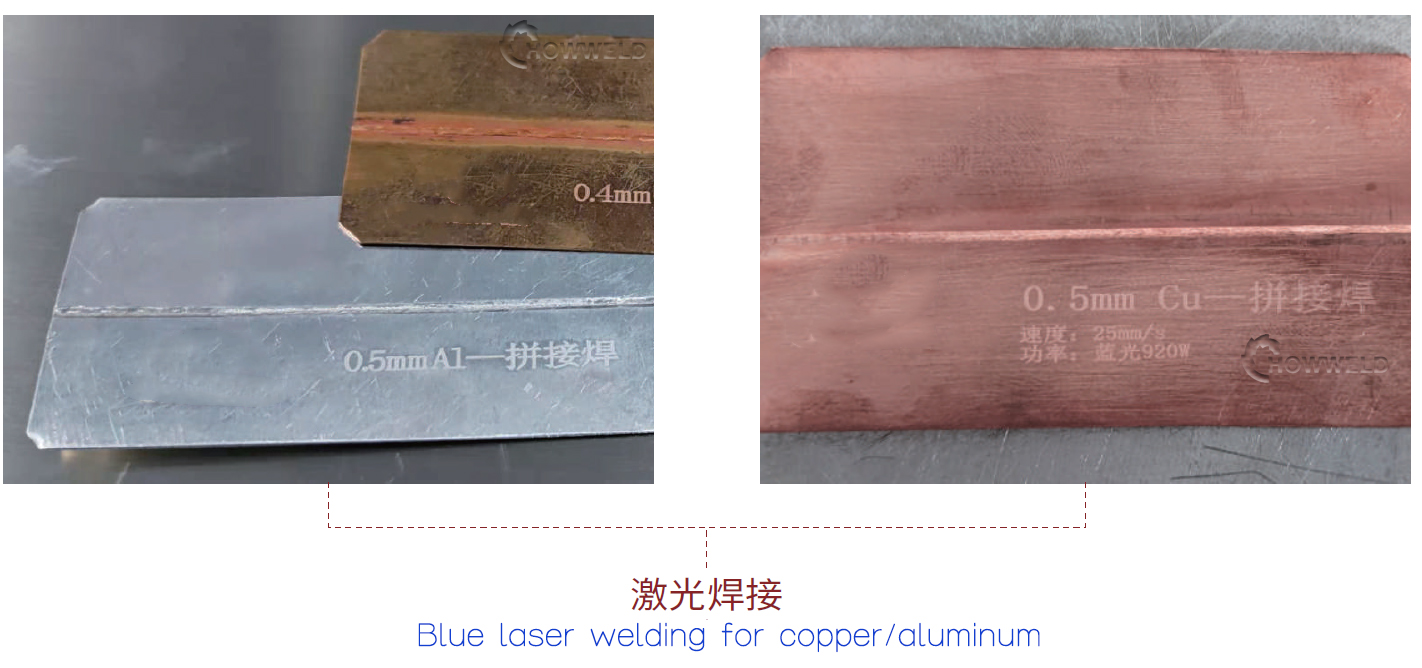
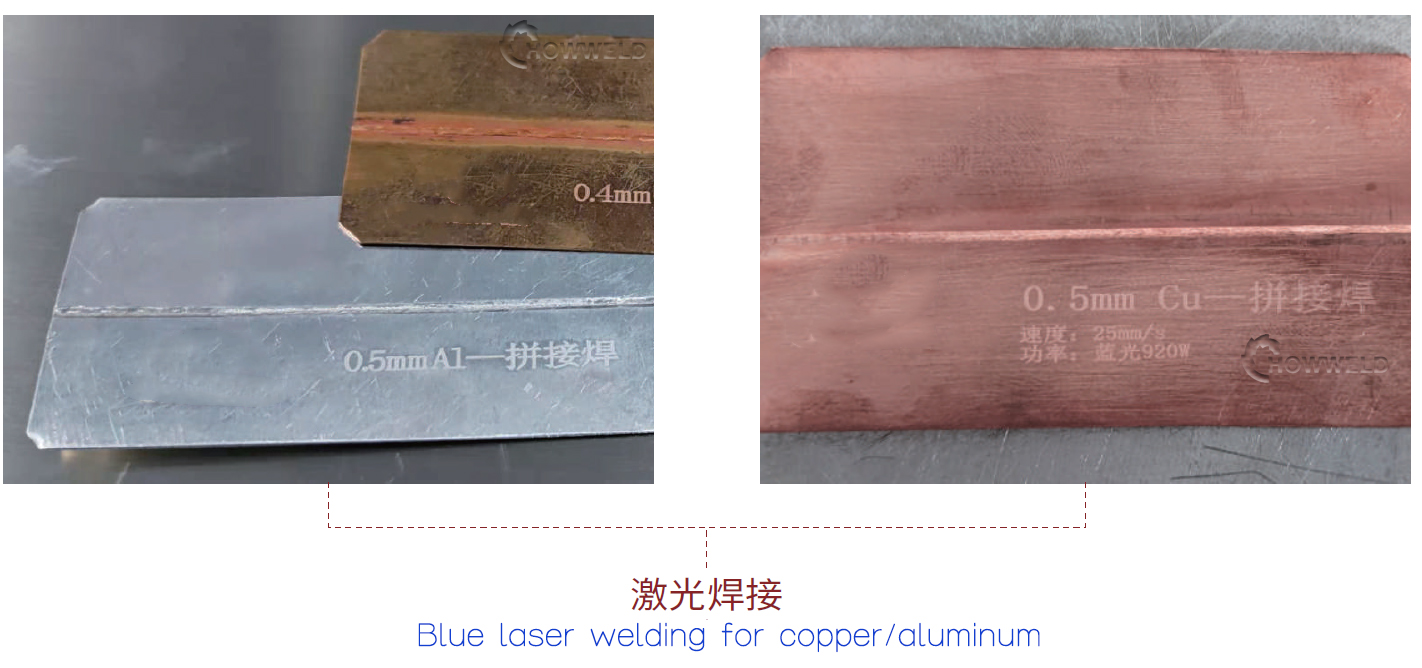
Blue light infrared composite welding technology, as an emerging welding technology, has advantages such as high efficiency, high precision, and environmental protection, and has broad application prospects in industrial production.
Above content writed by Howweld Team that we provide laser processing equipment with service, provide suitable laser welding, laser cleaning solution. Contact email: info@howweld.com
Welcome to inquire, visit and testing samples. We are looking forward to your presence.
With the continuous progress of technology, blue light infrared composite welding technology is expected to achieve higher welding efficiency and more accurate welding quality, bringing greater convenience and benefits to industrial production.