CNC automatic laser welding system for welding electronic cigarette heating mesh and pins
Time:2022-05-15
Views:848
Laser welding for electronic cigarette heating mesh and pins
The specific situation is: the width of the pin end of the heating mesh is 0.3mm, the thickness is 0.07mm, and the diameter of the cylindrical pin is 0.35mm. The welding requires the pin end of the heating mesh to be attached to the cylindrical pin. At the tangent of the two, laser welding Point through the heating mesh pin ends so that they are tightly soldered to the cylindrical pins.
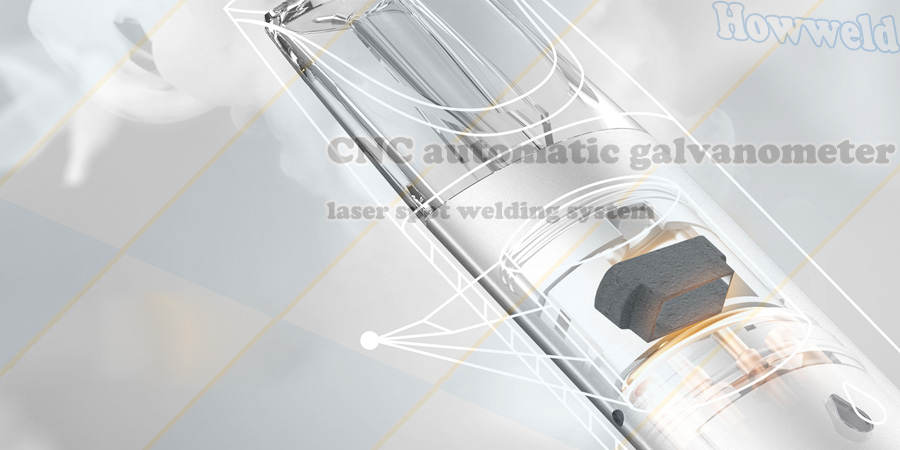
Electronic pods mainly refer to smoke-like tobacco products that match electronic cigarettes. HNB is a new type of tobacco product that has the feature of heating shredded tobacco or tobacco extract instead of burning shredded tobacco.
In order to prevent the smoke bomb from volatilizing faster, the Lesser Precision Plastic Laser Welder will be used to seal and weld the upper and lower layers of the smoke bomb‘s plastic casing.
A heating wire assembly in an electronic cigarette and a welding method. In this method, the heating wire components to be welded are heating wires and conductive wires wound on the oil absorption rope.
The method includes the following steps:
The first step is to remove the
The outer sheath of the connection end exposes the core wire inside the conductive wire;
The second step is to electrically connect a working electrode in the laser spot welding machine with the conductive wire;
The third step is to connect the core wire on the connecting end of the conductive wire to the connecting end of the heating wire and connect the other working electrode of the laser spot welding machine to the other working electrode at the same time.
Touch, the laser spot welder outputs current to weld the core wire on the connection end of the conductive wire and the connection end of the heating wire into one.
After welding with the above solution, the welding point will be small and firm after welding, and there will be no false welding phenomenon; the resistance change is small, the welding point will not generate heat energy conversion due to energization, and the welding point will not be corroded by smoke oil. Guarantee the characteristics of pure taste of smoke when absorbing oil.
First, the previous welding method:
1. The YAG laser machine using traditional technology, the YAG equipment has a large welding spot, the minimum solder joint diameter is generally greater than 0.4mm, the power fluctuation is large, unstable, the internal resistance test is unqualified, and the welding is not good enough.
2. The welding positioning position accuracy is poor.
3. The welding is offset, resulting in inaccurate welding points and extremely low welding efficiency.
Waste of production materials, waste of time, and increased cost input.
Second, the galvanometer lens spot welding machine precision laser welding machine launched by Howweld Company. Equipment welding range 200mm×100mm, According to the needs of solder joints, choose F-θ lens with focal length F=170mm.
3. Advantages
1. The welding spot is small, the diameter of the welding spot can be adjusted within 0.35mm, the energy density is concentrated, the welding is stable and the precision is high, the welding quality of the product appearance is improved, the energy of each welding spot is uniform, and the fluctuation range of the welding tensile strength is small, and the tensile strength is basically Consistent, the internal resistance test of the product is stable, and the resistance value is between 1.1Ω±0.1Ω, which meets the welding process requirements of the product.
2. The pins of the fixture are positioned with the positioning grooves, and the heating mesh is positioned with the positioning pins. The two use the negative magnetic attraction of magnets, so that the welding parts of each product fit tightly and have no gaps. The product is easy and fast to clamp and ensure the welding. Consistency of quality.
3. It can weld 300 solder joints at one time, and the welding is completed in 20 seconds. Compared with the traditional welding method, the efficiency is increased by at least 5 times, and the yield rate is more than 99% and stable.
Electronic smoke bomb plastic laser welding principle:
1. Fix two plastic parts with clamps.
2. The upper and lower jigs are closed, the parts are clamped together, and then the laser welding energy is used to pass through the first part, and then absorbed by the second part. The absorbed near-infrared laser is converted into heat energy, and the contact surface of the two parts is melted to form a welding area.Howweld cnc,works stable.
3. Apply pressure to make the welded area firm.
Advantages of electronic smoke bomb plastic laser welding:
(1) The energy is concentrated, and the excess energy consumption is extremely small.
(2) The volume of molten resin is small, and the excess resin chips are few.
(3) Since it is not a contact welding process, the loss and deformation of the machine can be minimized.
(4) The laser path can be controlled by a simple optical refraction principle, and is suitable for products of various shapes.
(5) The laser beam can be focused on a small area, and small and closely spaced parts can be welded.
(6) There are many kinds of weldable materials, and various dissimilar materials can also be joined to each other.
(7) Easy automatic high-speed welding, and can also be controlled by digital or computer.
(8) The laser source can be shared to multiple devices through the switching device.