How laser cladding works
Time:2023-02-17
Views:647
How laser cladding works
In many cases, laser cladding technology is being used in the repair and reconditioning of all types of mechanical equipment (Howweld). The most common traditional methods for metal cladding are all variations on the arc process.
In these industrial processes, an electric arc is established to melt the surface of the substrate material to a shallow depth. The cladding material is then introduced as wire or powder and melted by an electric arc to form the cladding.
In general, arc welding techniques provide an all-welded metallurgical bond with high strength, good impact properties and low porosity. However, the high heat input into the part will usually melt enough of the base material to allow substantial mixing of the base material into the cladding. This dilution is undesirable as it alters the properties of the chosen cladding material. In addition, high heat input causes mechanical deformations that require further processing after cladding to restore the dimensional accuracy of the part. This thermal stress leads to poorer mechanical quality, surface quality issues such as cracks and porosity, and shortened life of repaired parts. Microelectronics companies are pursuing the same general goal of reducing production costs while increasing yield and end product quality.
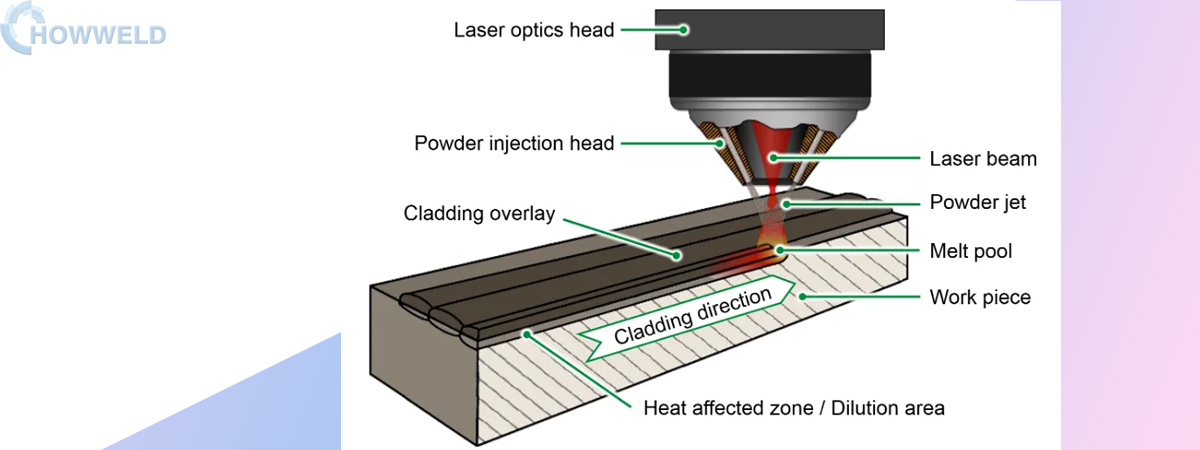
In general, arc welding techniques provide an all-welded metallurgical bond with high strength, good impact properties and low porosity. However, the high heat input into the part will usually melt enough of the base material to allow substantial mixing of the base material into the cladding. This dilution is undesirable as it alters the properties of the chosen cladding material. In addition, high heat input causes mechanical deformations that require further processing after cladding to restore the dimensional accuracy of the part. This thermal stress leads to poorer mechanical quality, surface quality issues such as cracks and porosity, and shortened life of repaired parts. Microelectronics companies are pursuing the same general goal of reducing production costs while increasing yield and end product quality.
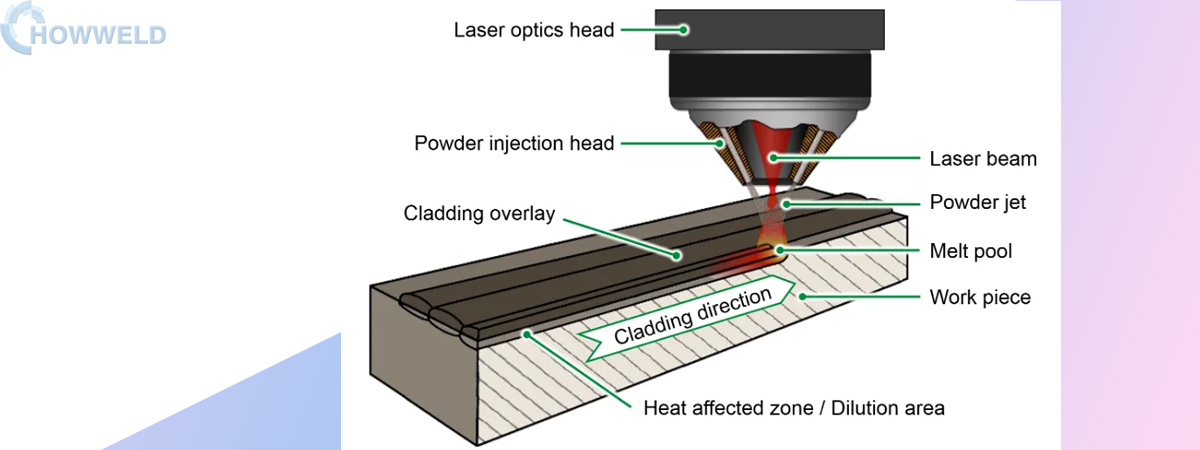
Lasers are driving this trend in many industries because of their ability to perform highly precise, non-contact processing. Cladding, in particular, is the process by which these purposes are achieved. The repair and refurbishment industry for production engineering is experiencing positive growth as the economic pressures to keep machinery running, thereby reducing our carbon footprint in landfills, change. With the rapid growth of laser applications and the reduction in the cost of laser systems, laser material processing is being successfully implemented in automotive, aerospace, shipbuilding and ship repair, oil and gas drilling, and many other industries.
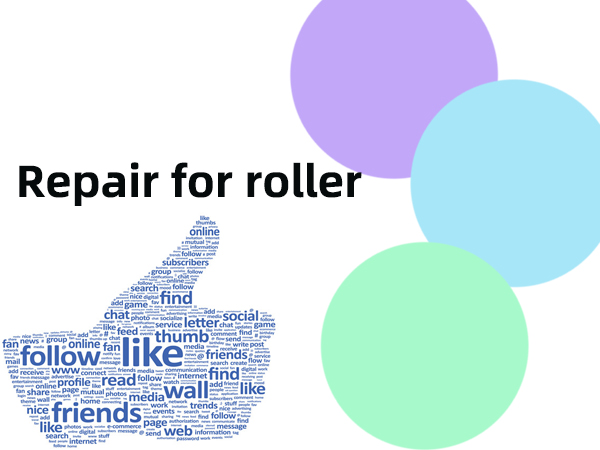
By definition, laser cladding is a method of depositing material by which powder or wire stock is melted and solidified using a laser to resurface or create near-net-shape parts, such as in additive manufacturing. In many cases, laser cladding technology is used in the repair and refurbishment of all types of machinery and equipment (Figure 1). The most common traditional methods of metal cladding are all variations of the electric arc process.
Powder jet laser cladding is a state-of-the-art welding technology that our company has been using extensively since 2012 and was the first to introduce this method to the Greek market. This procedure is widely used in the marine and industrial sectors such as rapid manufacturing, repair of spare parts, hardfacing/coating and many more applications. CNC cladding battery machines combined with laser cladding technology make everything repairable and viable.
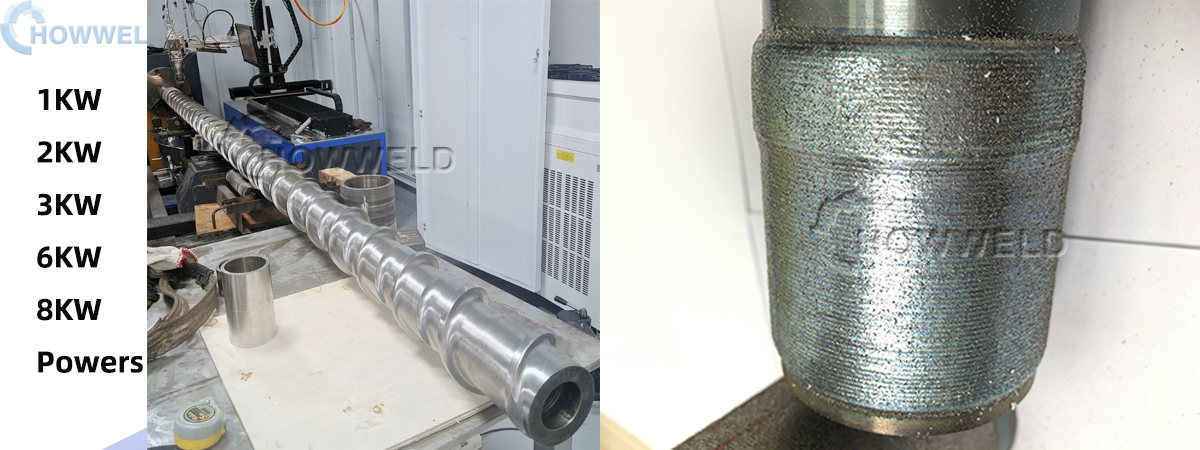
Powder jet laser cladding is a state-of-the-art welding technology that our company has been using extensively since 2012 and was the first to introduce this method to the Greek market. This procedure is widely used in the marine and industrial sectors such as rapid manufacturing, repair of spare parts, hardfacing/coating and many more applications. CNC cladding battery machines combined with laser cladding technology make everything repairable and viable.
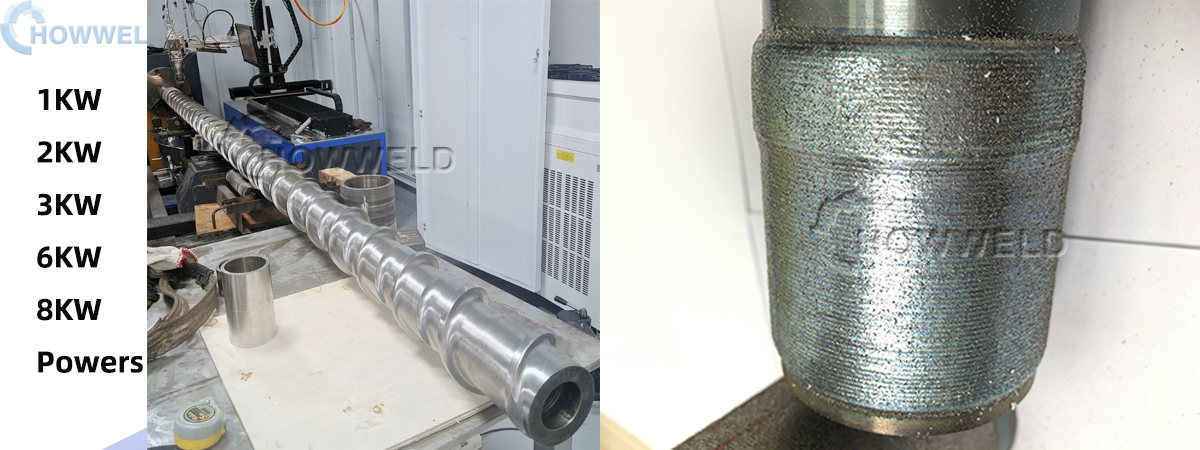
Benefits of laser cladding:
Metallurgical bond to the component enables the cover to resist impact and point loads
non-porous cover
The heat-affected zone is significantly smaller than that of traditional surfacing
Virtually no component deformation due to precisely controlled heat input
Up to 15% less dilution between part surface and weld overlay compared to conventional overlay
The thickness of each layer covering between 0.5 – 2mm can be precisely controlled
High repeatability and stability due to robot-controlled process
Can repair a wider range of component materials than conventional overlay welding
Due to the low heat input, heat treatment is usually not required after component repair
We are howweld company produced laser cladding machine manufacturers in China, provided laser cladding machine for repairing roller such as S45C, S50 steel roller.Manufacturer price offer laser hardening machine price cheaper to improve from 60hrc to 75hrc.leo@howweld.com
Hot Tags: laser cladding machine for repair roller and parts, howweld suppliers, manufacturers, factory, customized, wholesale, laser cladding equipment cost, laser hardening machine in stock, laser quenching for Mold Reparing Laser cladding machine 3000w 6000w
We are howweld company produced laser cladding machine manufacturers in China, provided laser cladding machine for repairing roller such as S45C, S50 steel roller.Manufacturer price offer laser hardening machine price cheaper to improve from 60hrc to 75hrc.leo@howweld.com
Hot Tags: laser cladding machine for repair roller and parts, howweld suppliers, manufacturers, factory, customized, wholesale, laser cladding equipment cost, laser hardening machine in stock, laser quenching for Mold Reparing Laser cladding machine 3000w 6000w