How to deal with air holes and thermal cracks in the process of laser welding aluminium alloy?
Time:2021-10-14
Views:1032
How to deal with air holes and thermal cracks in the process of laser welding aluminium alloy?
Aluminum alloy has the advantages of low density, high strength and good corrosion resistance. Therefore, it has been widely used in automobile industry, new energy, aerospace and construction industry.
At present, laser welding has been widely used in the production and manufacturing of aluminum alloy products.
Compared with traditional welding methods, laser welding can provide higher production efficiency, better weld quality, and realize high-precision welding and automation of complex structures.
Laser welding is a technology that radiates high-intensity laser to the metal surface, melts the metal through the thermal coupling between laser and metal, and then cools and crystallizes to form weld.
According to the thermal action mechanism of laser welding, it can be divided into thermal conductivity welding and deep penetration welding. Thermal conductivity welding is mainly used for packaging welding or micro nano welding of precision parts; Laser deep penetration welding is mainly used in the welding of materials requiring complete penetration.
The welding process will vaporize the materials and there will be keyholes in the molten pool. It is the most widely used laser welding method and the preferred method for aluminum alloy welding.
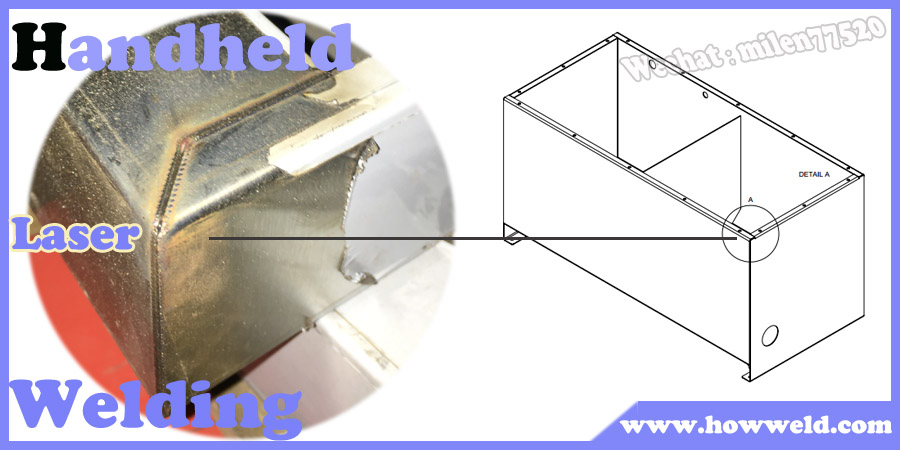
01 advantages:
Laser welding aluminum alloy adopts swing laser welding, without adding auxiliary materials, simple welding equipment, no consumables and easy automation.
02 disadvantages:
If the requirement for welding film is high, the weld is easy to sink; The starting point and end point of welding are easy to produce key points; The stability of welding process is general and welding defects are easy to occur.
03 case:
Construction and decoration industry - aluminum alloy door frame welding
Due to the inherent physical properties of aluminum alloy, such as low laser absorption, low boiling point of alloy elements, high thermal conductivity, high coefficient of thermal expansion, relatively wide solidification temperature range, high solidification shrinkage, low viscosity and high hydrogen absorption in liquid state, it is easy to produce defects such as pores and thermal cracks in the process of laser welding.
How to avoid this problem? Let Howweld team (www.howweld.com) tell you.
Among them, porosity is the most likely defect form in the process of aluminum alloy laser welding. It will destroy the compactness of weld metal, weaken the effective cross-sectional area of weld, and reduce the mechanical properties and corrosion resistance of weld.
Therefore, effective measures must be taken to prevent porosity and improve the internal quality of weld.
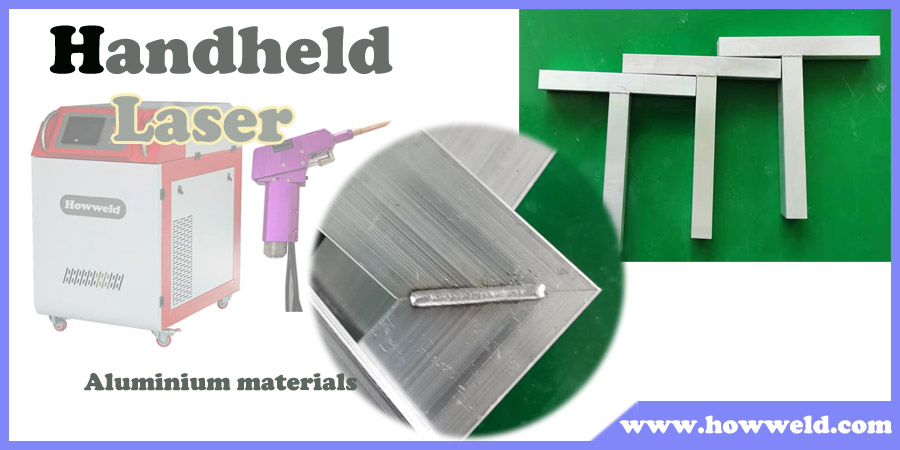
Ways of suppressing porosity in laser fusion welding
01 suppression of welding porosity by pre welding surface treatment
Pre welding surface treatment is an effective method to control the metallurgical porosity of aluminum alloy laser weld. Generally, the surface treatment methods include physical mechanical cleaning and chemical cleaning.
Through comparison, the process of chemical treatment of the surface of the test plate (metal cleaning agent cleaning - water washing - alkali washing - water washing - acid pickling - water washing - drying) is the best. The material surface thickness is removed by 25nah (sodium hydroxide) solution for alkali washing, and the residual alkali solution is neutralized by 20% hn03 (nitric acid) + 2% (hydrogen fluoride) aqueous solution for pickling.
The test plate is welded within 24 hours after surface treatment. When the test plate stays for a long time after treatment, it is assembled before welding and wiped with anhydrous alcohol.
02 suppression of welding porosity by welding process parameters
The formation of weld porosity is not only related to the surface treatment quality of weldments, but also related to welding process parameters.
The influence of welding parameters on weld porosity is mainly reflected in the weld penetration, that is, the influence of weld back width ratio on weld porosity.
The test shows that when the weld back width ratio r > 0.6, the centralized distribution of chain pores in the weld can be effectively improved. When the back width ratio r > 0.8, the existence of large pores in the weld can be effectively improved and the residual pores in the weld can be eliminated to a great extent.
03 suppression of welding porosity by correct selection of shielding gas and flow
The selection of shielding gas directly affects the welding quality, efficiency and cost. In the process of laser welding, the correct blowing of shielding gas can effectively reduce the weld porosity.
AR (argon) and he (helium) are used to protect the weld surface. In the process of aluminum alloy laser welding, the ionization degree of AR and he to the laser is different, resulting in different weld formation.
The results show that the porosity of the weld obtained by using AR as shielding gas is less than that of the weld when using he as shielding gas.
At the same time, we should also note that the gas flow is too small ((10L / min) and a large amount of plasma generated by welding cannot be blown away, which makes the welding molten pool unstable and increases the probability of pore formation. The gas flow is moderate (about 15L / min).
The plasma is effectively controlled, the shielding gas plays a good anti-oxidation role in the solution tank, and the pores are the least.
Excessive gas flow is accompanied by excessive gas pressure, which makes part of the shielding gas mixed into the solution tank and increases the porosity.
It has always been a difficult problem in the industry to suppress porosity defects in laser welding aluminum alloy. Affected by the properties of aluminum alloy materials, no porosity can be completely avoided in the welding process, but only the porosity can be reduced.
Through the process optimization before and after welding, we summarize and propose three ways to suppress porosity for the reference of colleagues in the industry.
Howweld not only focuses on the research and innovation of laser product technology, but also develops and explores various laser processing technologies, and looks forward to discussing with more industry experts to promote the improvement of laser processing technology in China.info@howweld.com