The miniaturization trend of fiber lasers
Time:2023-09-11
Views:496
The miniaturization trend of fiber lasers
In recent years, the 10000 watt laser has become a standard product in the industrial laser field, and the popularization of the 10000 watt laser has greatly improved the efficiency and capability boundary of industrial processing. However, as a large number of manufacturers flock to the Wanwa Circuit, homogeneous competition has also plunged this market into a red sea of "price wars". This environment has also caused the growth of China‘s fiber laser market to fall into a quasi stagnant situation of "seemingly rising but not rising".
Attempt to break the homogenization of fiber laser
To break this market dilemma, many companies have begun to seek differentiated competitive routes. At present, the three obvious paths for fiber lasers are high power, high brightness, and miniaturization.
High power has been the main theme of the development of fiber laser in the past few years. With the popularization of 10000 watt lasers, 30000 watt, 40000 watt, and 50000 watt have gradually entered the metal processing market. For the laser itself, the core difficulty lies in the power tolerance and long-term stability of the device; For practical applications, the lack of stable and reliable supporting components is the biggest obstacle to its development.
High brightness is actually the basic attribute of regression lasers. By increasing the energy density per unit area, the effect of replacing high power with high brightness and low power is achieved. At the same time, it has obvious advantages in fields such as high reflectivity material processing and advanced manufacturing. Its core difficulty lies in controlling mode instability and nonlinear effects.
Miniaturization is a key to opening up a new world of laser applications - smaller in size, lighter in weight, and more integrated, overturning past understanding of laser processing and giving birth to portable laser tools such as handheld laser welding and cleaning, greatly promoting the development of laser applications.
The miniaturization process of a 10000 watt laser
Due to the fact that fiber lasers can achieve power improvement through module stacking and beam merging, the overall volume of the laser is also continuously increasing during the process of fiber laser power improvement.
In 2017, a 6kW fiber laser with multiple 2kW modules combined entered the industrial market. In the following one or two years, 8kW, 12kW, 15kW, and 20kW lasers gradually appeared, but at that time, even 20kW lasers were combined on the basis of 2kW or 3kW, resulting in a huge volume of finished products. Although the performance has been improved, the excessive volume also brings significant trouble to users‘ transportation and assembly. With the increasing demand for 10000 watts, laser manufacturers are beginning to think about how to reduce the overall volume.
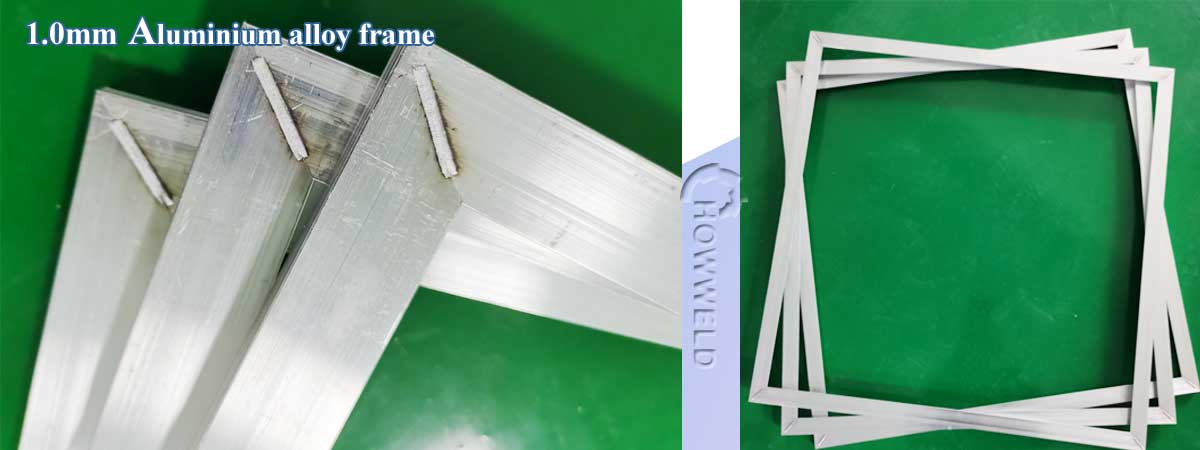
In 2017, a 6kW fiber laser with multiple 2kW modules combined entered the industrial market. In the following one or two years, 8kW, 12kW, 15kW, and 20kW lasers gradually appeared, but at that time, even 20kW lasers were combined on the basis of 2kW or 3kW, resulting in a huge volume of finished products. Although the performance has been improved, the excessive volume also brings significant trouble to users‘ transportation and assembly. With the increasing demand for 10000 watts, laser manufacturers are beginning to think about how to reduce the overall volume.
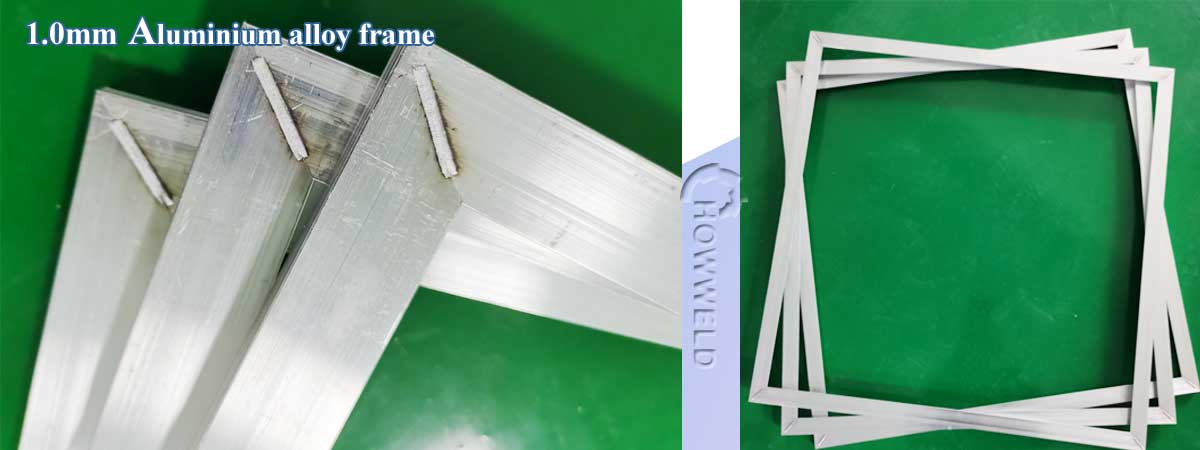
The main idea in the initial stage was to increase the power of a single laser module, gradually increasing the previous 3kW to 4kW and 5kW, and reducing the volume by reducing the number of beam combining modules for a 10000 watt laser. However, at this stage, the sudden decrease in the number of modules and the sudden increase in single module power pose significant challenges to the stability of the laser cores.
As the above challenges are gradually overcome, another major advantage of single module lasers begins to emerge - without the need for beam merging, the beam quality is greatly improved, and its performance is significantly improved compared to multimode lasers in fields such as sheet metal processing and precision manufacturing. As a result, high-power single module lasers began to become independent products integrated with laser equipment.
At this stage, domestic laser manufacturers have made extensive optimizations and improvements for the application scenarios and optical characteristics of single module lasers. After several years of effort, a single module 12kW laser was introduced. Compared to a multimode 12KW laser, a single module 12kW laser reduces its volume by about 60%, reduces its weight by about 40%, and has a processing capacity comparable to 15kW on certain materials. It can be said that the core idea at this stage is to replace multimode combiner lasers with smaller single module lasers in some application scenarios.
In the already small 1500W and 2000W power ranges, the Lightning series has reduced its volume by 40% and weight by 25%, while the 3000W power range has reduced its volume by nearly 75% and weight by 50%. The 6000W power range with the most significant changes has reduced the volume of the lightning laser by nearly 90% and reduced its weight by nearly 75% compared to the old model laser! The "big brother" of the Lightning series, the Lightning 12KW fiber laser, has reduced its volume by 75% and weight by 60% compared to the old single module laser.
Expanding the territory of miniaturized lasers
It can be said that this disruptive volume reduction has a huge impact on the downstream market, with the most obvious being the handheld laser welding market. The early handheld laser welding machine was equipped with a chiller and an old-fashioned 1000W single module laser, with a cabinet volume of 1.05m3 (equivalent to the volume of an old-fashioned washing machine). With the market explosion in recent years and users‘ demand for portability, smaller and more portable have become the consistent pursuit of handheld welding manufacturers. Through the disruptive "bone shrinking" lightning series laser, it is possible to install two handheld welding machines in one trunk.
For sheet metal processing users, this new form of drawer design allows the laser to be shipped with a complete set of equipment, truly achieving ready to use after disassembly. It also allows users to say goodbye to traditional and occupied laser air conditioning rooms, and can save more than 30% of equipment installation time.
Another focus that has attracted people‘s attention is the significant increase in shipping costs in 2022, which has increased the transportation costs of export enterprises. The significant reduction in laser volume means that the number of lasers that can be loaded in the same container increases significantly, and it also means that the number of containers required for the same number of lasers decreases, which can save a lot of shipping costs for enterprises. Especially overseas agents can gain greater competitive advantages due to reduced logistics costs.
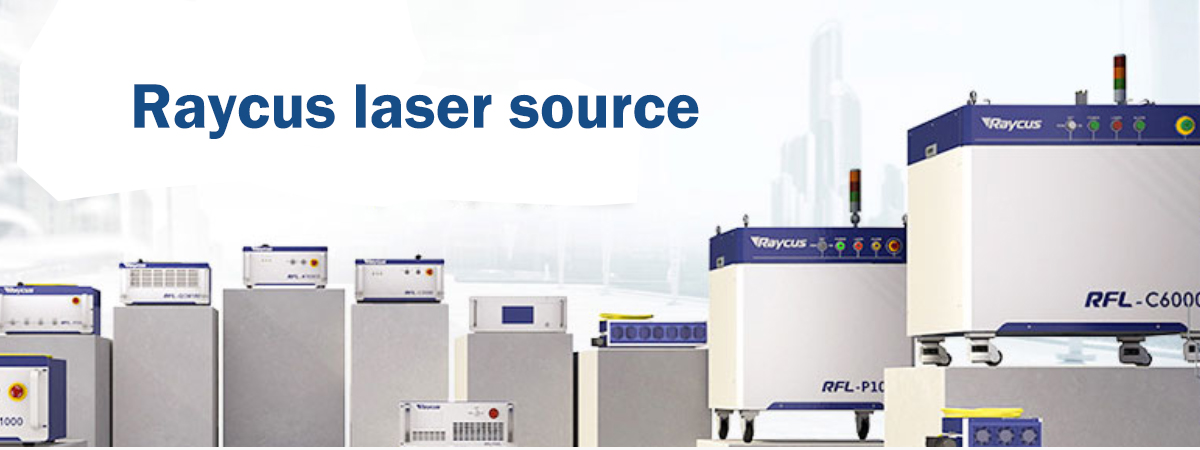
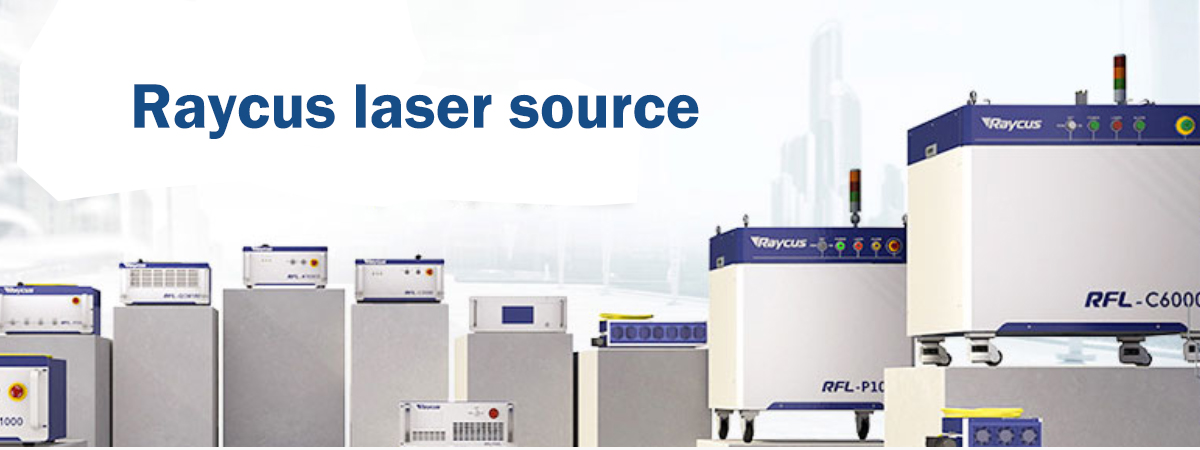
Why can lightweight lasers succeed?
Firstly, the stability of the pump source. The fourth generation industrial pumping technology has become the core guarantee for the stability of the Lightning series lasers.
Highly integrated and modular design, comprehensively upgrading the pump source, optical path system, thermal control management, and electronic control system, can effectively reduce the pressure of thermal management. Combined with a stable and reliable forced water circulation thermal control management scheme and optimized cooling system design, the advantages of active fiber optic heat dissipation and overall structural temperature control effectively ensure the long-term stability of laser output power and wavelength.
In terms of intelligence, the Bluetooth centralized control function enables real-time monitoring of device status, working parameters, and fault warning, thereby reducing device failure rate and improving device stability.
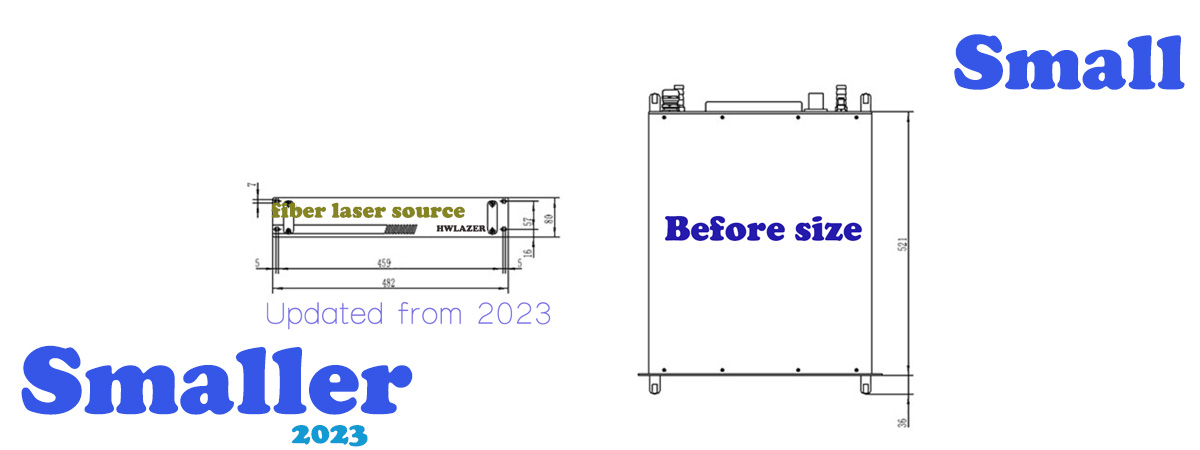
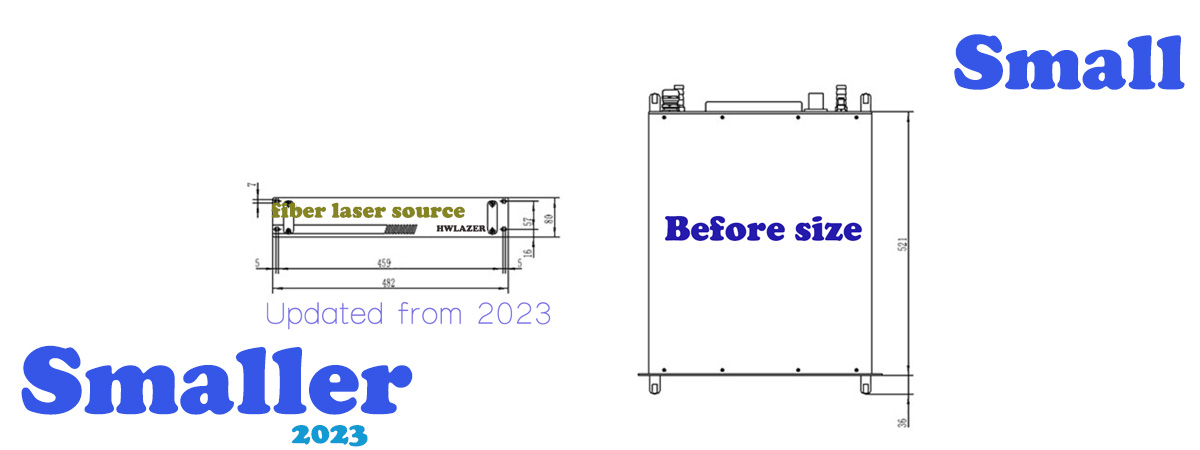
Above content writed by Howweld Team that we provide laser processing equipment with service, provide suitable laser welding, laser cleaning solution. Contact email: info@howweld.com
Welcome to inquire, visit and testing samples. We are looking forward to your presence.