How to treat the surface of stainless steel products after welding?
Time:2021-08-27
Views:1093
How to treat the surface of stainless steel products after welding?
For stainless steel products and stainless steel furniture, there are signs of black spots on the surface of the welding interface at the beginning; using pickling passivation solution can remove the extremely thin chromium-containing metal at the beginning of passivation. Therefore, the chemical methods of pickling and electrolytic polishing can restore the corrosion resistance of stainless steel in welds and other surface damage.
Let Howweld manager (www.howweld.com)give you a detailed introduction.
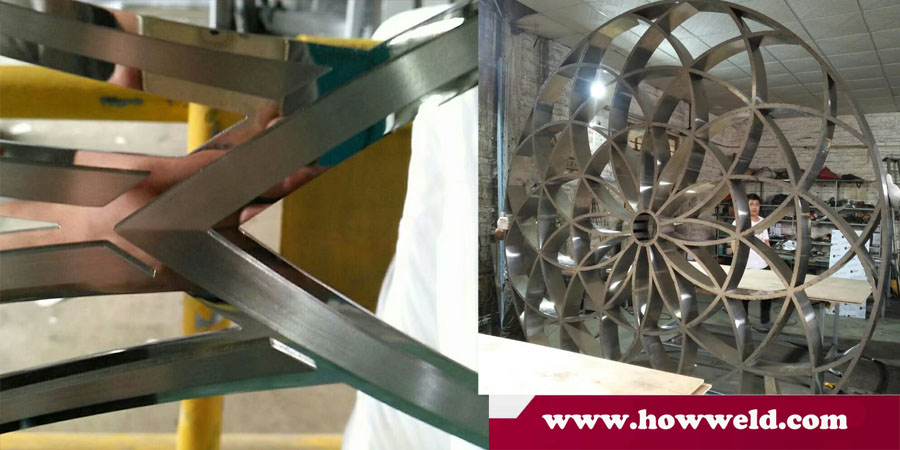
Let Howweld manager (www.howweld.com)give you a detailed introduction.
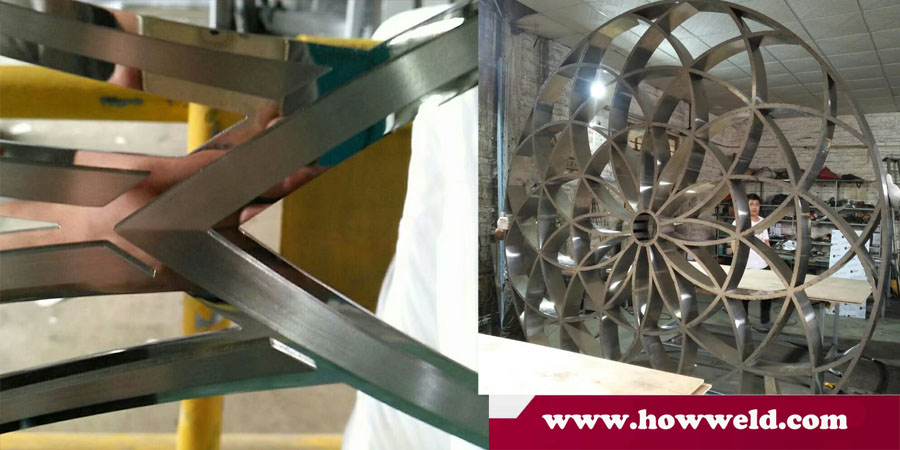
Firstly. Introduction to stainless steel varieties
1. The main components of stainless steel: generally contain high-quality metal elements such as chromium (Cr), nickel (Ni), molybdenum (Mo), and titanium (Ti).
2. Common stainless steel: chromium stainless steel, containing Cr≥12%; nickel-chromium stainless steel, containing Cr≥18%, containing Ni≥12%.
3. Classification from the metallographic structure of stainless steel: There are austenitic stainless steels, such as: 1Cr18Ni9Ti, 1Cr18Ni11Nb, Cr18Mn8Ni5. Martensitic stainless steel, such as: Cr17, Cr28, etc. Generally referred to as non-magnetic stainless steel and magnetic stainless steel.
Two, common stainless steel welding surface treatment methods.
1. Commonly used stainless steel welding surface treatment technology has the following treatment methods: ① surface natural whitening treatment; ② surface mirror bright treatment; ③ surface coloring treatment.
2. Whitening treatment of natural surface color: In the process of processing, stainless steel undergoes coiling, binding, welding, or artificial surface fire-roasting and heating treatment to produce black oxide scale. This kind of hard gray-black oxide scale is mainly composed of NiCr2O4 and NiF two kinds of EO4 components. The previous one. 3. Sandblasting (pill) method: mainly uses the method of spraying micro glass beads to remove the black oxide scale on the surface.
3. Chemical method: Use a non-polluting pickling passivation paste and a non-toxic cleaning solution with inorganic additives at room temperature for immersion. So as to achieve the purpose of whitening the natural color of stainless steel. After processing, it basically looks like a dull color. This method is more suitable for large and complex products.
4. Surface mirror bright treatment method after stainless steel welding: According to the complexity of stainless steel products and the different requirements of users, mechanical polishing, chemical polishing, electrochemical polishing and other methods can be used to achieve mirror gloss.
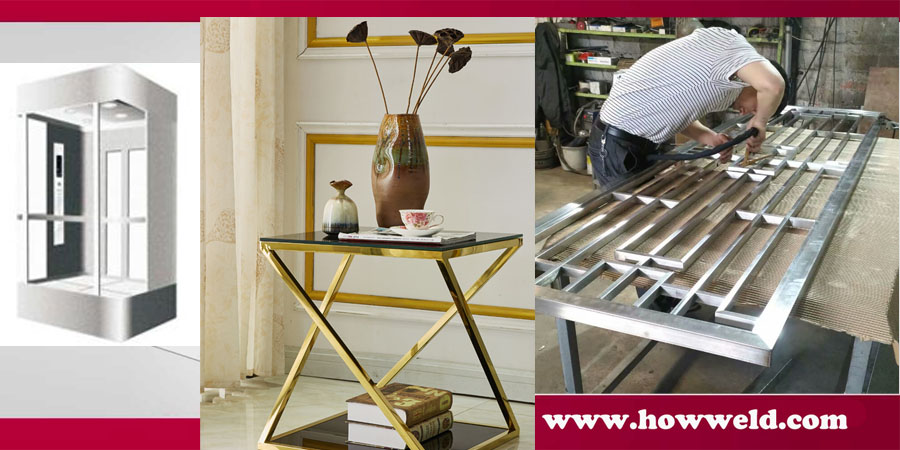
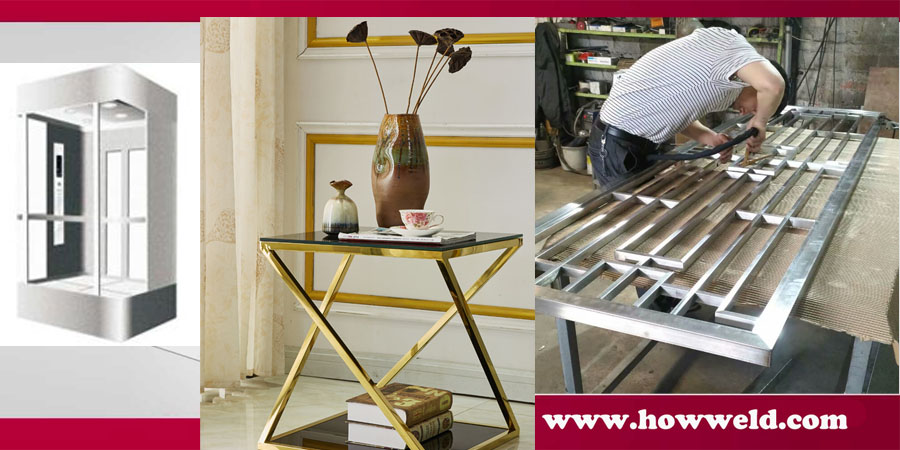
The advantages and disadvantages of these three methods are as follows:
1. Stainless steel surface coloring treatment: stainless steel coloring not only imparts various colors to stainless steel products, increases the variety of products, but also improves the wear resistance and corrosion resistance of the products.
Three. There are several coloring methods for stainless steel:
⑴Chemical oxidation coloring method: It is the color of the film formed by chemical oxidation in a specific solution. There are dichromate method, mixed sodium salt method, vulcanization method, acid oxidation method and alkaline oxidation method. Generally "INCO" (INCO) is used more, but if you want to ensure the color of a batch of products are consistent, you must use a reference electrode to control.
⑵Electrochemical oxidation coloring method: In a specific solution, the color of the film is formed by electrochemical oxidation.
⑶Ion deposition oxide coloring method: Place the stainless steel workpiece in a vacuum coating machine for vacuum evaporation plating. For example: titanium-plated watch cases and watch bands are generally golden yellow. This method is suitable for mass product processing. Because of the large investment and high cost, small batch products are not economical.
⑷High-temperature oxidation coloring method: In a specific molten salt, the workpiece is immersed in a certain process parameter to make the workpiece form a certain thickness of oxide film, and present a variety of different colors.
⑸ Vapor-phase pyrolysis coloring method: more complicated, less application in industry.
Four, stainless steel welding post-treatment method selection: according to the product structure, material, and different requirements on the surface, select the appropriate method for treatment. The treatment method is mainly polishing and pickling passivation. The surface of stainless steel will be oxidized after welding, and the surface treatment is to clean the oxide layer and achieve a beautiful effect.
Five, the common causes of corrosion of stainless steel parts:
1. Surface pollution: oil, dust, acid, alkali, salt, etc. attached to the surface of the workpiece are transformed into corrosive media under certain conditions, and chemically react with certain components in the stainless steel parts, resulting in chemical corrosion and rust.
Surface scratches: Various scratches damage the passivation film, which reduces the protective ability of stainless steel, and it is easy to react with chemical media, produce chemical corrosion and rust.
Cleaning: After pickling and passivation, the remaining liquid will remain and the stainless steel will be directly corroded (chemical corrosion) if the cleaning is not clean.
2. Electrochemical corrosion
Carbon steel pollution: scratches and corrosive media caused by contact with carbon steel parts form a galvanic cell and cause electrochemical corrosion.
Cutting: The adhesion of rusty substances such as cutting slag, splash and corrosive media to form galvanic cells and produce electrochemical corrosion.
Roasting: The composition and metallographic structure of the flame heating area change unevenly, and form a galvanic cell with the corrosive medium to produce electrochemical corrosion.
Welding: physical defects (undercuts, pores, cracks, lack of fusion, incomplete penetration, etc.) and chemical defects (large grains, chromium depletion at grain boundaries, segregation, etc.) in the welding area form galvanic cells with corrosive media to cause electrochemical corrosion .
Material: Chemical defects (uneven composition, S, P impurities, etc.) and surface physical defects (loose, blisters, cracks, etc.) of the stainless steel material are conducive to the formation of galvanic cells with corrosive media and electrochemical corrosion.
Passivation: Poor pickling and passivation results in uneven or thin passivation film on the surface of stainless steel, which is prone to electrochemical corrosion.
Cleaning: The remaining acid pickling passivation residue and the chemical corrosion products of stainless steel form electrochemical corrosion with stainless steel parts.
Finally, there are one more method to do,it is laser cleaning machine can clean spots after laser welding. Handheld welding for stainless steel with faster welding speed,and 360 degree to weld,very easy operation.
After laser cleaning the surface of the product, it needs polishing treatment.
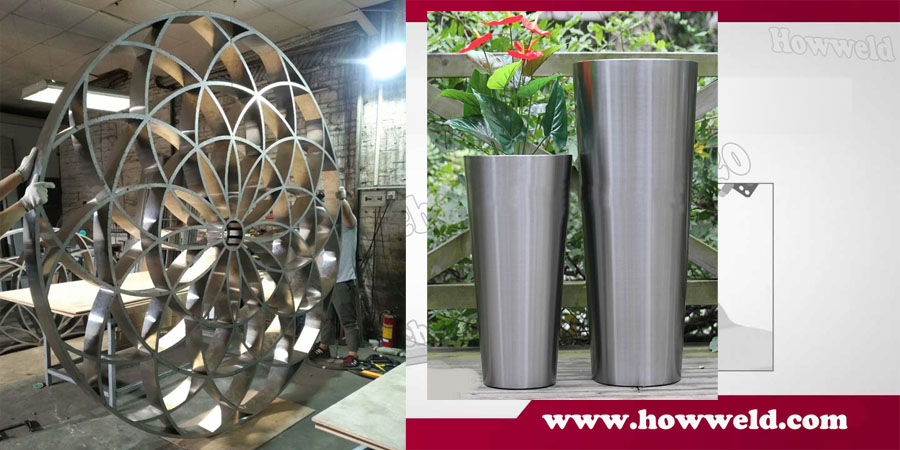
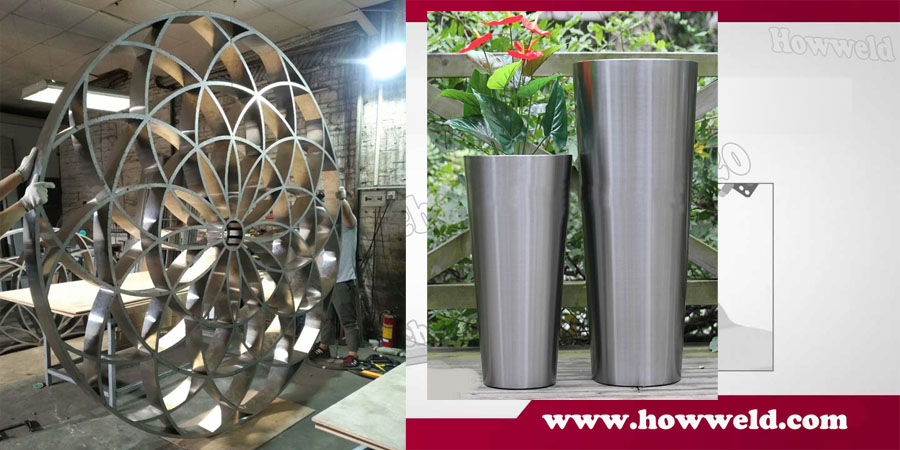
In short, due to its special metallographic structure and surface passivation film, stainless steel is generally difficult to be corroded by chemical reaction with the medium, but it is not impossible to be corroded under any conditions. In the presence of corrosive media and incentives (such as scratches, splashes, cutting slag, etc.), stainless steel can also be corroded by slow chemical and electrochemical reactions with corrosive media, and the corrosion rate is quite fast under certain conditions. Rust phenomena, especially pitting and crevice corrosion. The corrosion mechanism of stainless steel parts is mainly electrochemical corrosion.
Therefore, all effective measures should be taken during the processing of stainless steel products to avoid rust conditions and inducements as much as possible. In fact, many rust conditions and inducements (such as scratches, splashes, cutting slag, etc.) also have significant adverse effects on the appearance of products, and they should and must be overcome.
The above content comes from Howweld.A famous laser equipment manufacturer in China,persistently promote the application of laser equipment in various industries,to provide customers with the most suitable solution.Welcome to inquire, visit and testing samples.Email:info@howweld.com
Hope this article can help you all. (www.howweld.com) Thank you for your attention.
Hope this article can help you all. (www.howweld.com) Thank you for your attention.