What can laser cladding machine do?
Time:2023-04-14
Views:735
Laser cladding technology
Laser cladding refers to placing the selected coating material on the surface of the clad substrate by different feeding methods. After laser irradiation, it melts with a thin layer on the substrate surface at the same time, and forms a very low dilution after rapid solidification.
Laser cladding refers to placing the selected coating material on the surface of the clad substrate by different feeding methods. After laser irradiation, it melts with a thin layer on the substrate surface at the same time, and forms a very low dilution after rapid solidification.
The laser cladding machine assembled by howweld has stable performance. The surface coating combined with the substrate metallurgically can significantly improve the wear resistance, corrosion resistance, heat resistance, oxidation resistance and electrical characteristics of the base surface, so as to achieve the purpose of surface modification or repair, which not only meets the requirements for the specific properties of the material surface, but also saves a lot of precious elements.
Compared with surfacing, spraying, electroplating and vapor deposition, laser cladding has the characteristics of small dilution, dense structure, good combination between coating and substrate, many suitable cladding materials and large changes in particle size and content. Therefore, the application prospect of laser cladding technology is very broad. Howwell team believes that laser cladding brings a good way to repair the mold and re realize its own value to the product.
Synchronous laser cladding is to send the cladding material directly into the laser beam to complete the feeding and cladding at the same time. Cladding materials are mainly fed in the form of powder, and some also use wire or plate for synchronous feeding.
The main process flow of preset laser cladding is: substrate cladding surface pretreatment - preset cladding material - preheating - Laser Melting - post heat treatment.
The main process flow of synchronous laser cladding is: substrate cladding surface pretreatment - feeding laser melting - post heat treatment.
Application industry
1、 Surface modification of materials, such as gas turbine blades, rolls, gears, etc;
2、 Repair the surface of products, such as rotors, molds, etc.
3、 Rapid prototyping. Using the layer by layer sintering superposition of metal powder, the model is quickly manufactured. Rapid manufacturing of parts by Laser Cladding Technology.
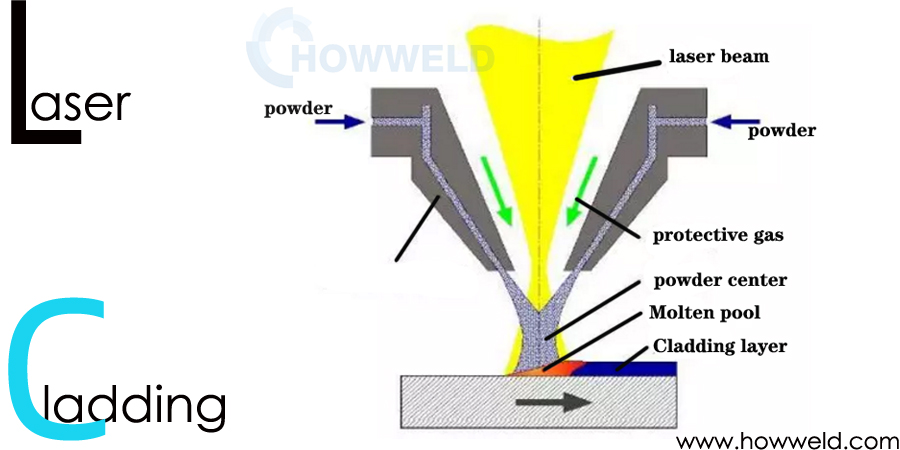
Components in the drilling, exploration and extraction of Oil & Gas are exposed to severe wear corrosion and erosion. Reliability of these components in critical to mitigate lost production time and significant financial losses.
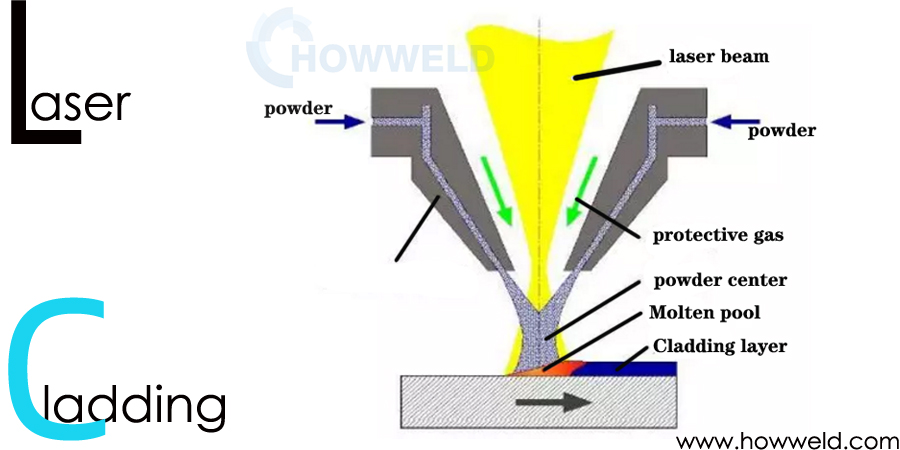
Components in the drilling, exploration and extraction of Oil & Gas are exposed to severe wear corrosion and erosion. Reliability of these components in critical to mitigate lost production time and significant financial losses.
These tough drilling environments require the best protection and surface technologies to extend the life of critical oilfield tools; providing superior protection against abrasion, erosion and corrosion.
The key beneficial properties of laser cladding is integral to this protection and results in improved reliability, long life, and reduced down time.
Laser cladding is fast becoming the industry standard in the oil and gas field.
Laser cladding is realized in the form of metal wire (laser hot wire cladding) or powder cladding. The laser beam forms a molten pool on the surface of the workpiece, and the laser coating material (wire or powder) melted by the laser is added to it. The exposure time is very short. Because the cooling is very fast, only a short delay will occur. The result is that one layer is metallurgically connected with the base material. It is tougher than the coating formed by thermal spraying, and it is harmless to health compared with hard chromium coating, for example.
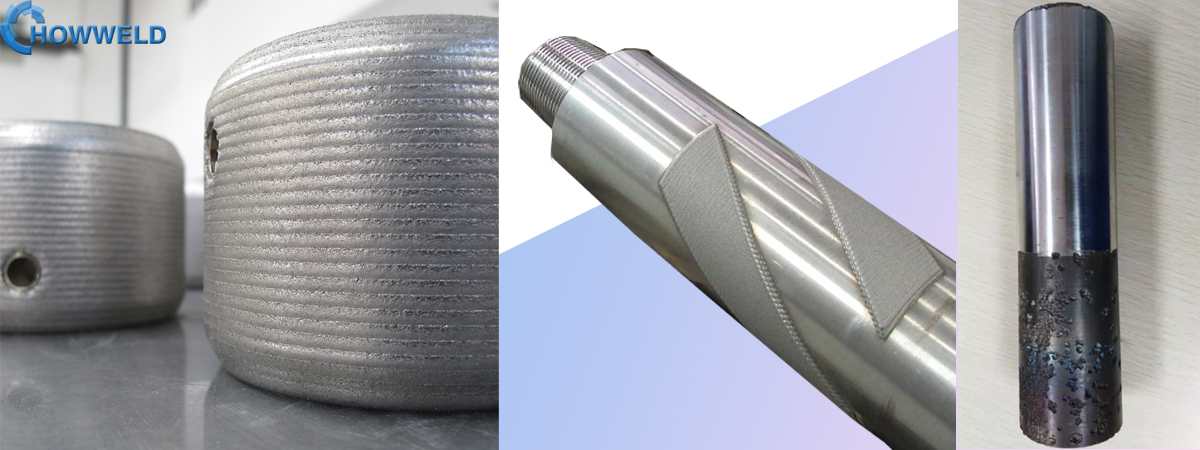
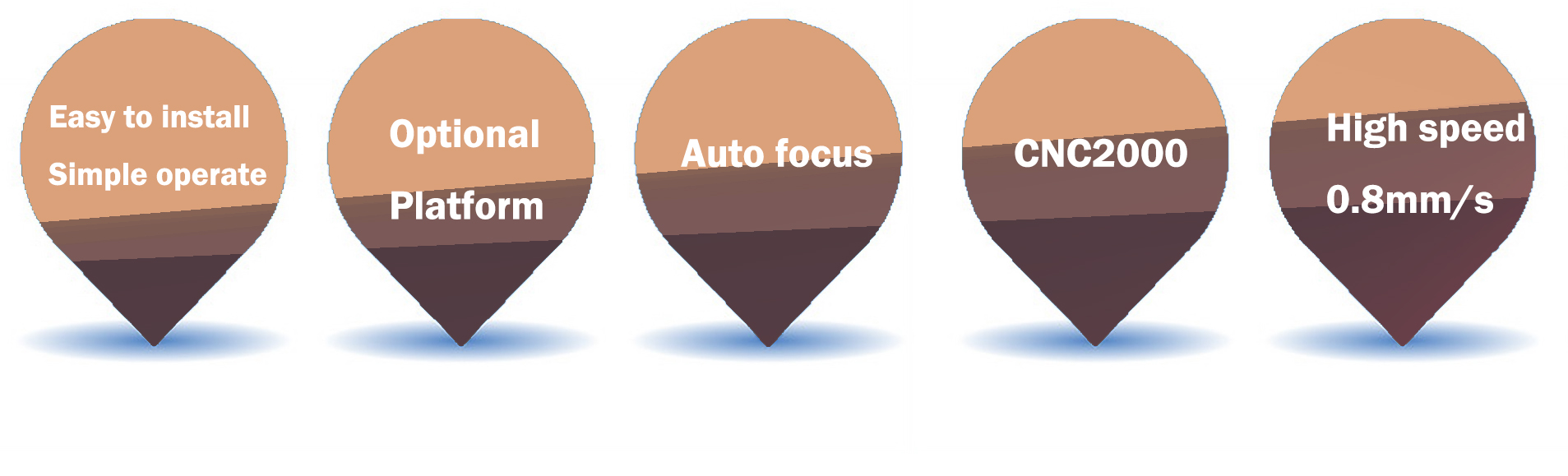
Laser cladding is realized in the form of metal wire (laser hot wire cladding) or powder cladding. The laser beam forms a molten pool on the surface of the workpiece, and the laser coating material (wire or powder) melted by the laser is added to it. The exposure time is very short. Because the cooling is very fast, only a short delay will occur. The result is that one layer is metallurgically connected with the base material. It is tougher than the coating formed by thermal spraying, and it is harmless to health compared with hard chromium coating, for example.
Laser cladding technology is a new technology with high economic benefits. It can prepare high-performance alloy surfaces on cheap metal substrates without affecting the properties of the substrate, reduce costs, and save precious and rare metal materials. Therefore, it is widely used in the world All industrially advanced countries attach great importance to the research and application of laser cladding technology. The application of laser cladding is mainly in two aspects, namely corrosion resistance (including high temperature corrosion resistance) and wear resistance. It has a wide range of applications, such as the sealing surface of valves and valve seats of internal combustion engines, water, gas or steam separators. Laser cladding, etc. The following introduces the common application industries of laser cladding technology.
The application of laser cladding repair involves metallurgy, electric power, petroleum, chemical industry, shipbuilding, locomotive, coal machinery, automobile and other pillar industries of the national economy. According to the working conditions of different equipment, laser surface remanufacturing (cladding repair, additive manufacturing) processing mainly improves the wear resistance, corrosion resistance, high temperature resistance, oxidation resistance and other properties of metal parts, not only can make the failed parts Return to service and significantly extend the life of new parts.
Common application industries of laser cladding technology
1. Manufacture and remanufacture of electrical equipment and its components
The distribution of power equipment is large and the operation is uninterrupted, and the probability of damage to its components is high. The steam turbine is the core equipment of thermal power generation. Due to the special working conditions of high temperature and high heat, it is necessary to repair the damaged unit parts every year, such as the shaft diameter of the main shaft of the steam turbine and the moving blades. Gas turbines are often damaged due to their high temperature conditions of up to 1300 °C. Using laser remanufacturing technology to repair all its defects and restore its performance, the cost is only 1/10 of the price of the new unit.
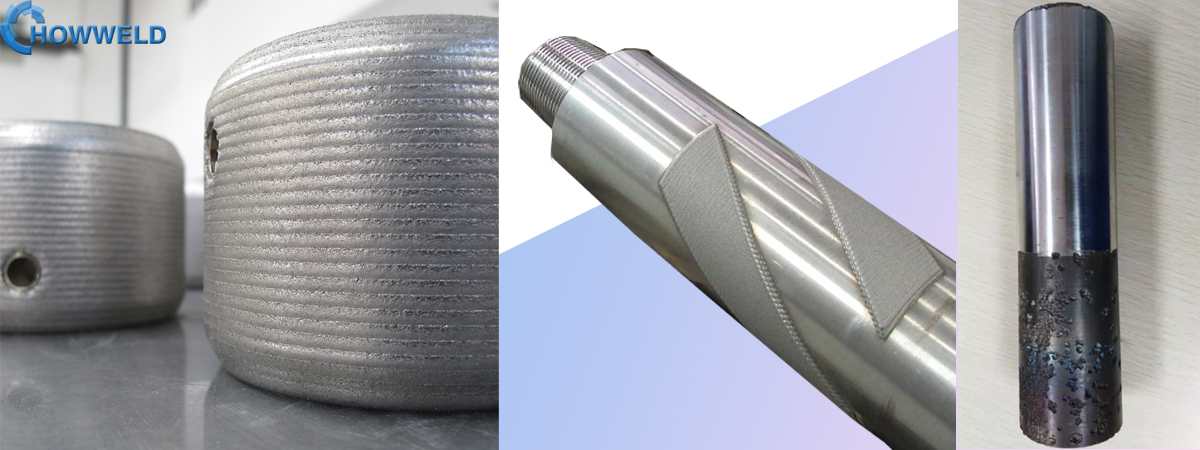
2. Automotive field
In the application of the automobile industry, laser technology was first used mainly for cutting and heat treatment. With the development of cladding technology, it gradually developed into flexible additive manufacturing technology. For example, the sealing tapered surface of the exhaust valve of the engine is clad with Stellite alloy, which is the first automobile part to adopt this technology. The annular surface of the Italian Fiat car engine exhaust valve seat and the American car exhaust valve seat are all made of laser cladding heat-resistant alloy. At present, Beijing Jike Guochuang Lightweight Science Research Institute cooperates with Guangxi Yuchai to carry out cladding and forming of wear-resistant and high-temperature resistant alloys on the annular surface of engine valve seats, and has also achieved initial results.
3. Marine ship direction application
The marine environment is harsh, with high humidity and high salinity, and marine ship equipment is prone to wear and corrosion. Offshore engineering equipment and ship components are technically complex and valuable, and the waste of failure and scrapping is huge. Domestic shipyards have used laser cladding technology to repair the corrosion of ship impellers, engine cylinder liners, and cone surface wear of diesel engine intake and exhaust valve discs with high precision, and achieved good cladding effects, restored functions and improved wear resistance. Corrosion resistance.
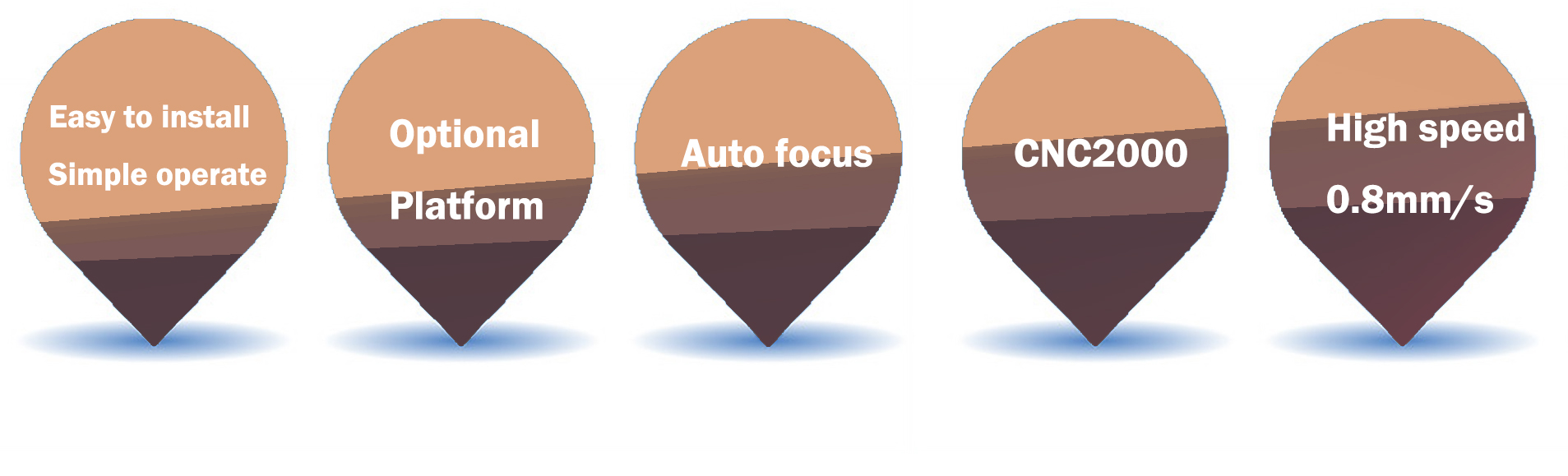
4. Manufacture and remanufacture of petrochemical equipment and its parts
The modern petrochemical industry basically adopts a continuous mass production mode. During the production process, the machine works in a harsh environment for a long time, resulting in damage, corrosion, and wear to the components in the equipment. The parts that often cause problems include valves. , pumps, impellers, journals, wheels, disks, bushings, bearing bushes, etc. of large rotors, and these components are very expensive, and there are many types of parts involved, most of which are complex in shape, and are difficult to repair. But because of the emergence of laser cladding technology, these problems are not a problem.
5. Application in steel industry
Rolls are consumables in the production of rolling mills. The quality of the roll directly affects the efficiency and product quality of the rolling mill, so it has high technical requirements for repair. Usually, the failure modes of rolls include thermal cracking, spalling, fatigue wear, abrasive wear and so on. Using laser cladding technology, according to the roll material, working environment and technical requirements, select the corresponding cladding alloy powder and cladding process, the cladding layer and the base material achieve good metallurgical bonding, the cladding layer has a dense and fine structure, and the surface hardness can be guaranteed Reaching 50-60HRC, it has played a very good role in strengthening and repairing. The performance of the repaired roll surface, such as wear resistance and impact resistance, is several times higher than that of the traditional repair process, and the price is about 1/3 of the new roll.
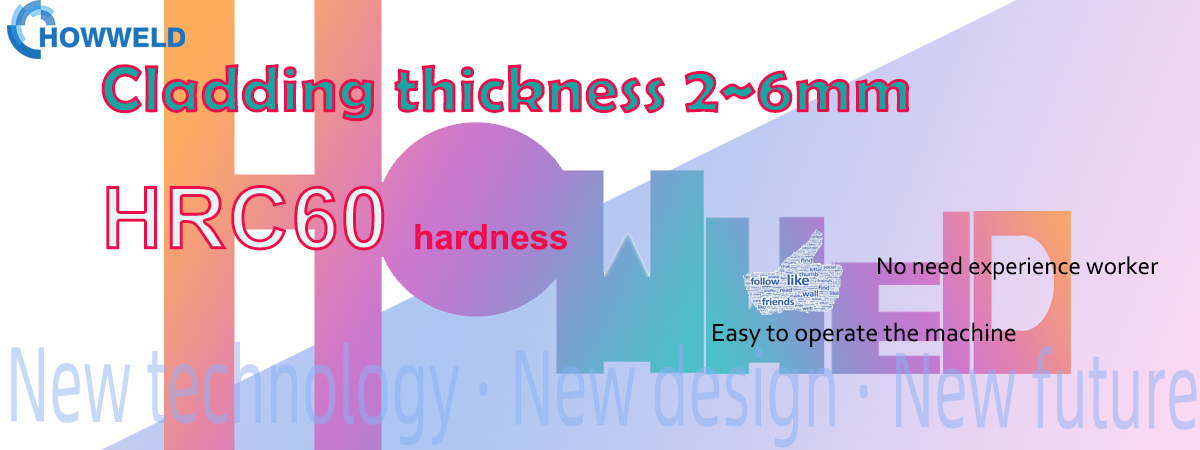
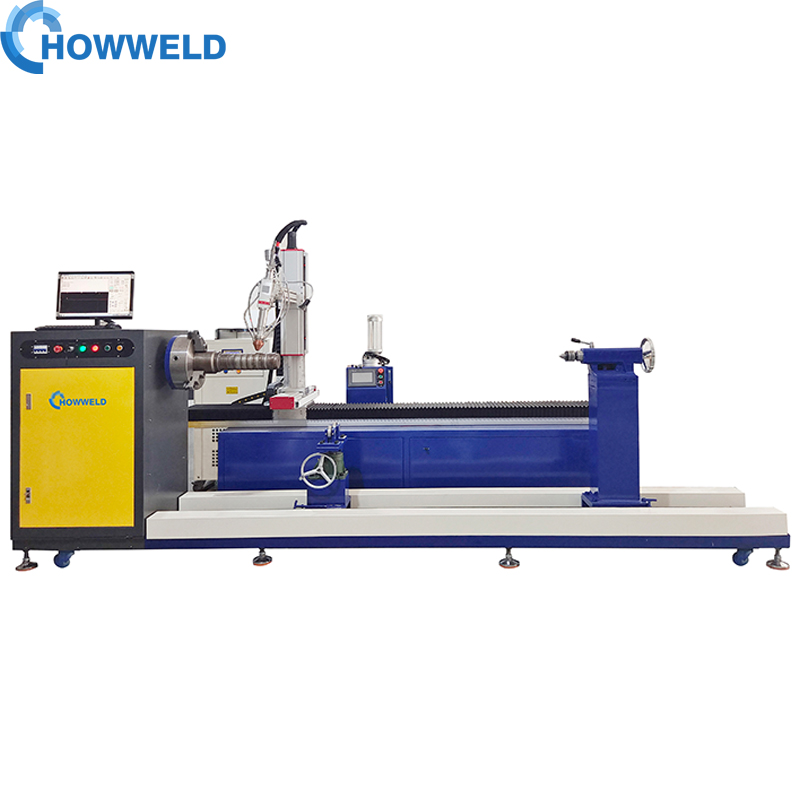
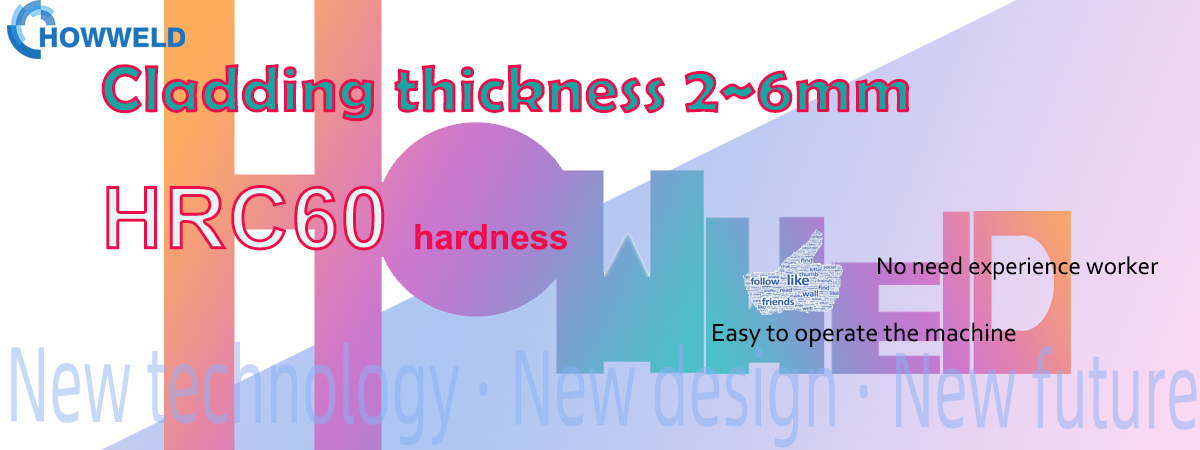
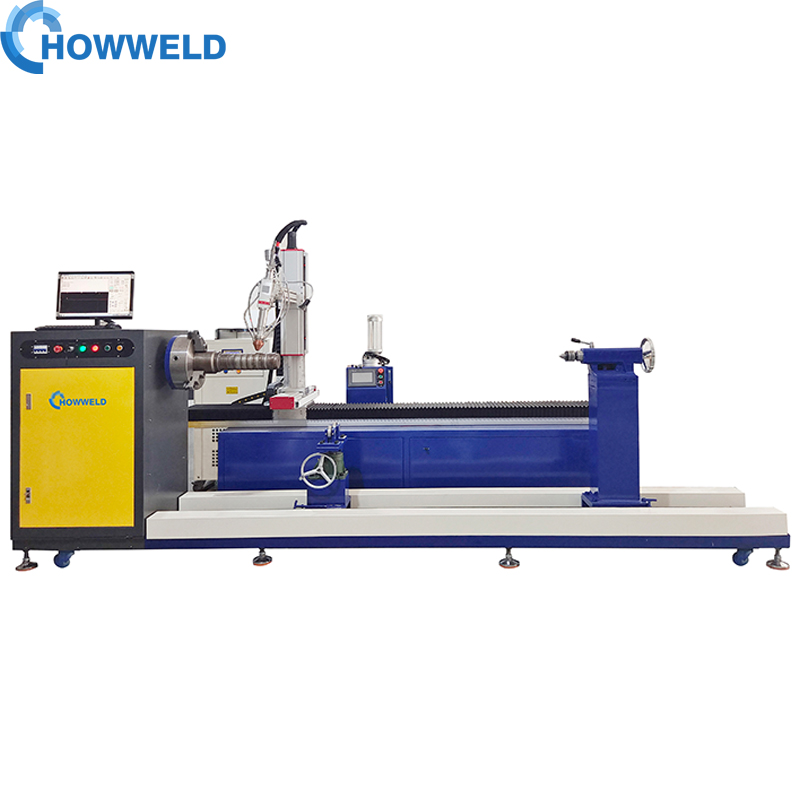
Above content writed by Howweld Team that we provide laser processing equipment with service, provide suitable laser welding, laser cleaning solution. Contact email: info@howweld.com
Welcome to inquire, visit and testing samples. We are looking forward to your presence.
Keywords:
Repairing large molds is no longer a problem
Keywords:
Main shaft diameter and moving blade of steam turbine
Gas turbine blade, roll, gear
laser cladding machine
howweld laser cladding
fiber laser cladding head
fiber laser cladding machine
laser cladding machine yag
metal powder for laser cladding machine