Copper sheets split joint cnc laser welding solution_How to weld copper_Howweld
Time:2023-12-26
Views:527
How To Weld Copper - Blue laser hybrid fiber laser welding process double beam
The thermal conductivity of copper is too high, almost 5 times that of pure iron and 1.7 times that of pure aluminum. The traditional arc welding method has insufficient power density and the welding effect is not ideal. Laser welding has the characteristics of high power density, fast welding speed, and small welding heat impact, and is considered a suitable process for copper connections.
At present, the most common and mature laser for material processing applications is infrared laser with a wavelength between 760nm and 1mm, and its frequency is between microwave and visible light. However, the absorption rate of infrared laser by solid copper is only 3~5%, and it is difficult to form a stable molten pool in the initial stage of welding. Therefore, infrared laser still faces certain challenges in copper welding. In recent years, in order to solve the problem of low absorption rate of copper infrared laser welding, people have gradually turned their attention to visible light lasers with wavelengths in the shortwave band (300-600nm). As the wavelength becomes shorter, the material absorption rate can be greatly increased. For example, copper‘s absorption rate of blue light with a wavelength of 450nm is as high as about 65%, which is 13 times that of infrared laser. Therefore, short-wavelength visible lasers show great potential for fast, high-quality welding of copper.
This article summarizes the research progress of laser melting welding technology of copper and its alloys in recent years, introduces the infrared laser, visible light laser and dual-beam composite laser welding technology of copper, compares the advantages and disadvantages of different processes, and finally compares the advantages and disadvantages of visible light laser welding and The application of hybrid welding technology is prospected to provide reference for research on laser welding process of copper and its alloys.
Simply using infrared laser for linear welding of copper has an unstable process window and maximum penetration fluctuation, and is prone to defects such as spatter, melt ejection, and holes.
Bubble formation at the tip of a small hole is one mechanism responsible for defects such as melt splatter and holes. The high reflectivity of the copper surface causes the laser energy to be significantly concentrated inside and below the small hole. Eventually, the inside of the small hole surrounded by the molten pool will expand excessively, increasing the instability of the small hole and the molten pool, leading to the formation of welding defects.
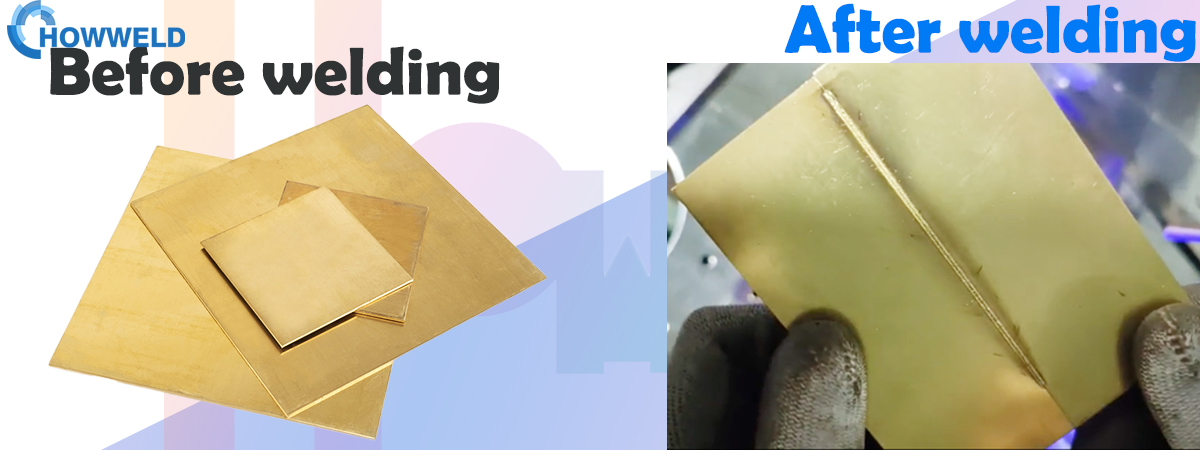
Green laser is a kind of visible light with a wavelength of 500-560nm. The absorption rate of copper for green light with wavelength λ = 515nm is as high as 40%, which is about 8 times the infrared light absorption rate of about 1um. The energy coupling efficiency is higher and it has no effect on surface oxidation. The degree of sensitivity is also reduced. Compared with infrared laser, the use of green laser can significantly reduce the threshold power of copper deep penetration welding. The amount of melt spray and spatter on the weld surface is small, and it is almost unaffected by the welding speed. The effect of infrared laser welding is strongly dependent on the welding speed, and molten splash and spatter increase sharply as the welding speed decreases.
Infrared laser sources are more sensitive to changes in welding speed and laser power than green light. Compared with infrared single laser and two-in-one fiber laser, the weld penetration fluctuation produced by green laser is smaller, and the stability of heat conduction and deep penetration welding transition is higher.
Since green lasers with wavelengths of 515nm and 532nm rely on their nonlinear optical crystals to convert pump laser energy into energy at the target wavelength, the conversion process will result in higher power loss, and the lasers require complex cooling systems and complex optical settings. , lasers are expensive and inefficient. Blue laser semiconductor lasers based on gallium nitride materials can directly produce lasers with a wavelength of 450nm without further frequency doubling. They have the advantages of simple structure, easy use, electro-optical conversion efficiency, and high absorption rate. Therefore, the industry has focused its attention on On to the blue semiconductor laser.
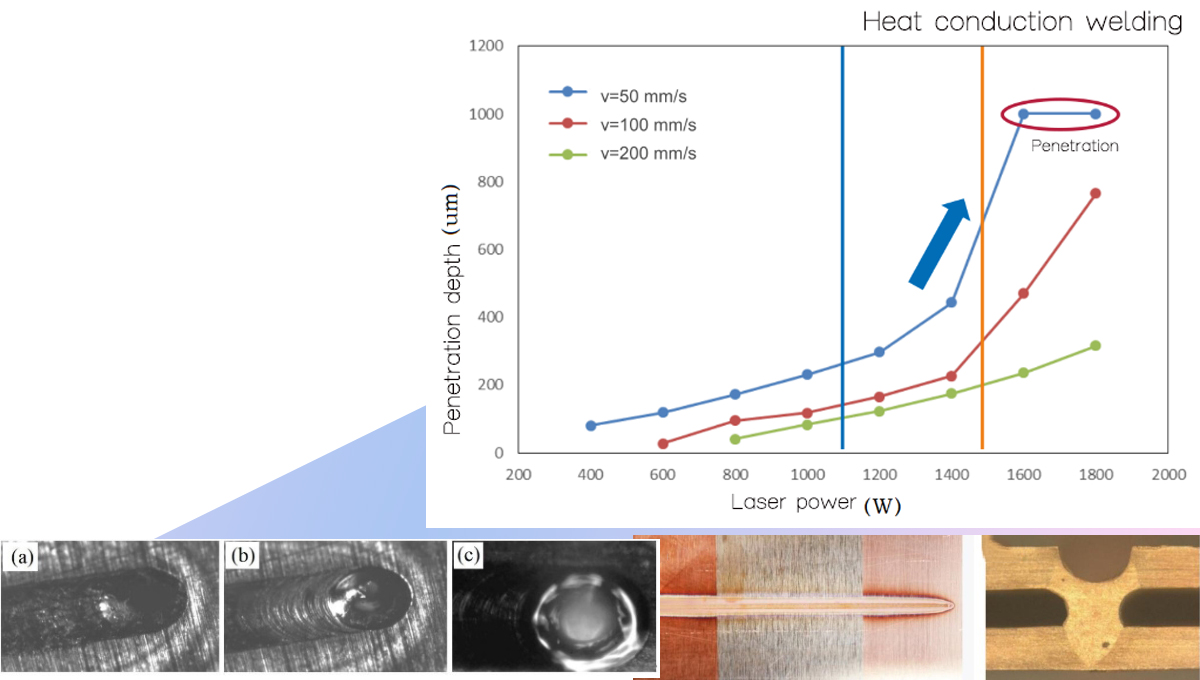
The absorption rate of copper metal for infrared light at room temperature only accounts for 3-5%, and it has high thermal conductivity. Therefore, infrared laser welding of copper is difficult and the spatter is serious; although by using annular beam distribution , can improve the welding effect to a certain extent, but its own characteristics determine that it is difficult to completely avoid problems such as energy waste and spatter during the welding process. In addition, infrared laser is very sensitive to factors such as oxidation, oil stains, and roughness of the copper surface, making the processing economical. Safety, efficiency and stability are all subject to certain constraints. In addition, the excessive return light of copper to infrared lasers can damage optical components and cause personnel safety hazards. Therefore, the development of shorter wavelength laser light sources and welding processes will be the development direction to completely solve the difficulty of copper laser welding.
It can be seen that with the continuous development and breakthroughs of semiconductor laser chips and beam combining technology, the power and beam quality of blue lasers will gradually increase, and the cost will gradually decrease. By then, blue lasers will gradually replace infrared lasers in the field of highly reflective material welding industry. .
1. Copper has low absorption rate of infrared laser and is prone to problems such as welding spatter, molten metal splash, pores and large fluctuations in penetration depth. Through high power density lasers, combined with high welding speed (≥15m/min), swing welding or spatial power modulation and other measures, the infrared laser welding process of copper can be stabilized and the occurrence of welding defects can be reduced.
2. Green light and blue light visible light laser welding of copper has the advantages of high absorption rate and high energy coupling efficiency. It is less sensitive to the surface quality of the material and can achieve spatter-free heat conduction welding. The welding process is more stable and the process repeatability is higher. However, visible light lasers currently have problems such as low power and high price, which greatly limits their large-scale application.
3. Using the infrared-visible light dual-beam composite welding process, using a smaller power visible light laser, the infrared laser can achieve "forced deep penetration welding" of copper when it is lower than the "deep penetration welding threshold power", and significantly reduce Welding spatter, low equipment cost and high welding quality have very outstanding advantages and good application prospects.
Above content writed by Howweld Team that we provide copper welding laser processing equipment with service, provide suitable laser welding, laser cleaning solution. Contact email: info@howweld.com
Welcome to inquire, visit and testing samples. We are looking forward to your presence.