The output power of a laser operating in continuous wave mode does not vary over time.
Pulse Laser
Pulse laser refers to a laser with a single laser pulse width less than 0.25 seconds and only operates once every certain interval of time. It has a high output power.
QCW Laser
Quasi-continuous wave (QCW) fiber lasers utilize relatively long pulses of high laser power to achieve processing results similar to that of continuous wave (CW) lasers with lower average power.
Quasi-CW pulses provide peak power up to 10X average power and are able to offer up to hundreds of joules of pulse energy.
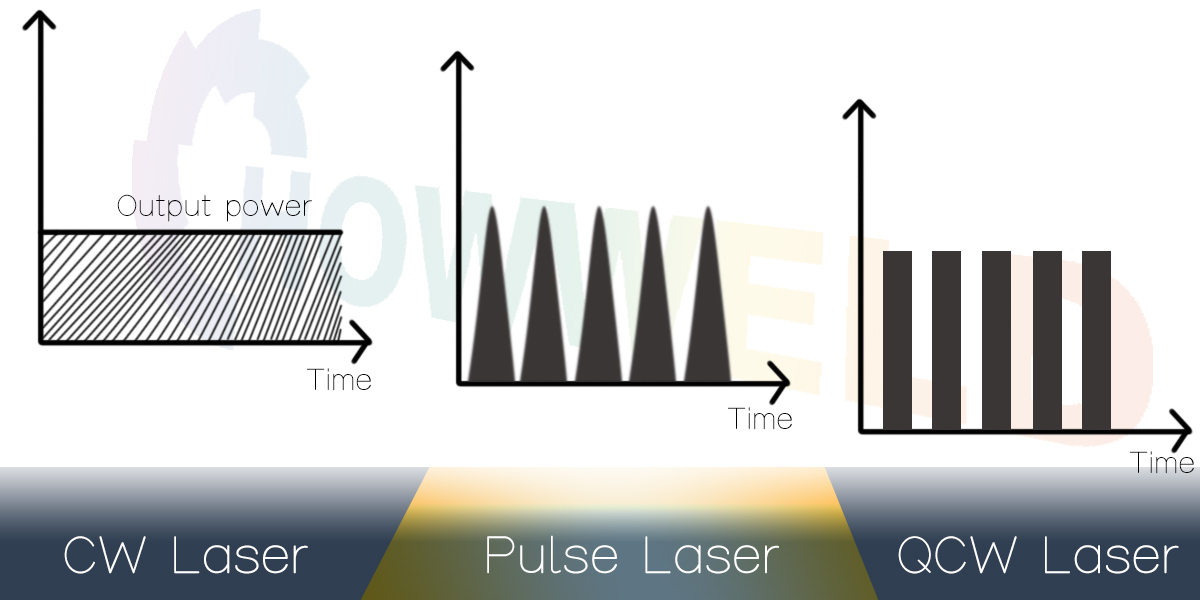
QCW Laser CNC Welding (Quasi-Continuous Wave) is a laser welding technology that combines aspects of both continuous wave (CW) and pulsed laser systems. It delivers high peak power in short bursts or pulses while maintaining the ability to operate in quasi-continuous mode, making it an efficient and versatile option for various industrial applications. Here’s an overview:
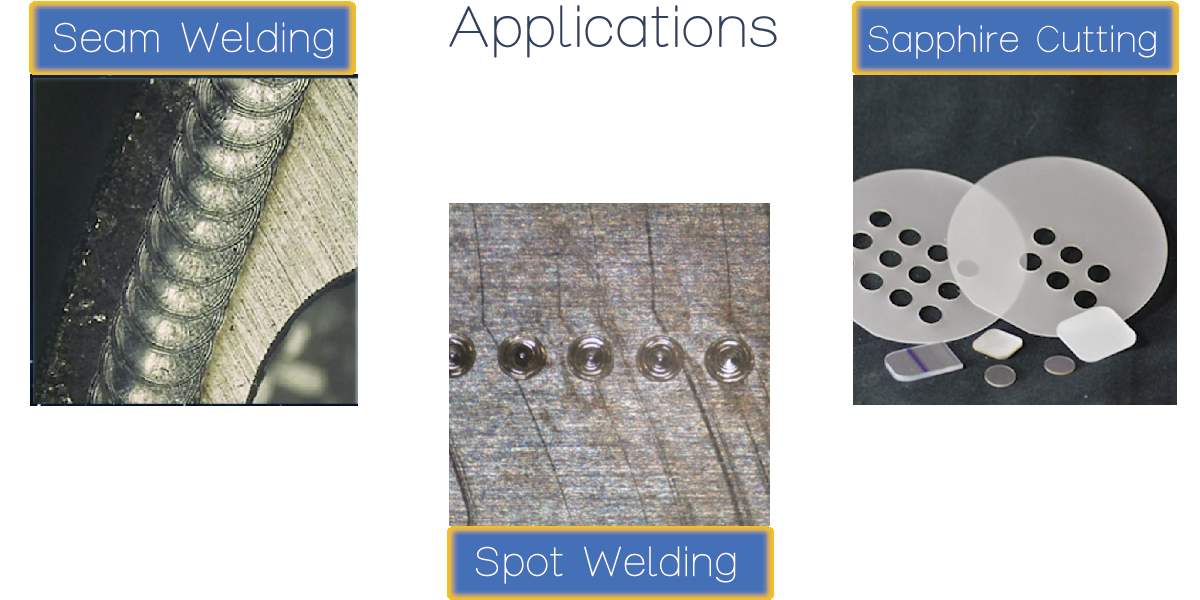
4. Materials Suitable for QCW Laser Welding
5. Key Features
6. Limitations
7. QCW vs CW Laser Welding
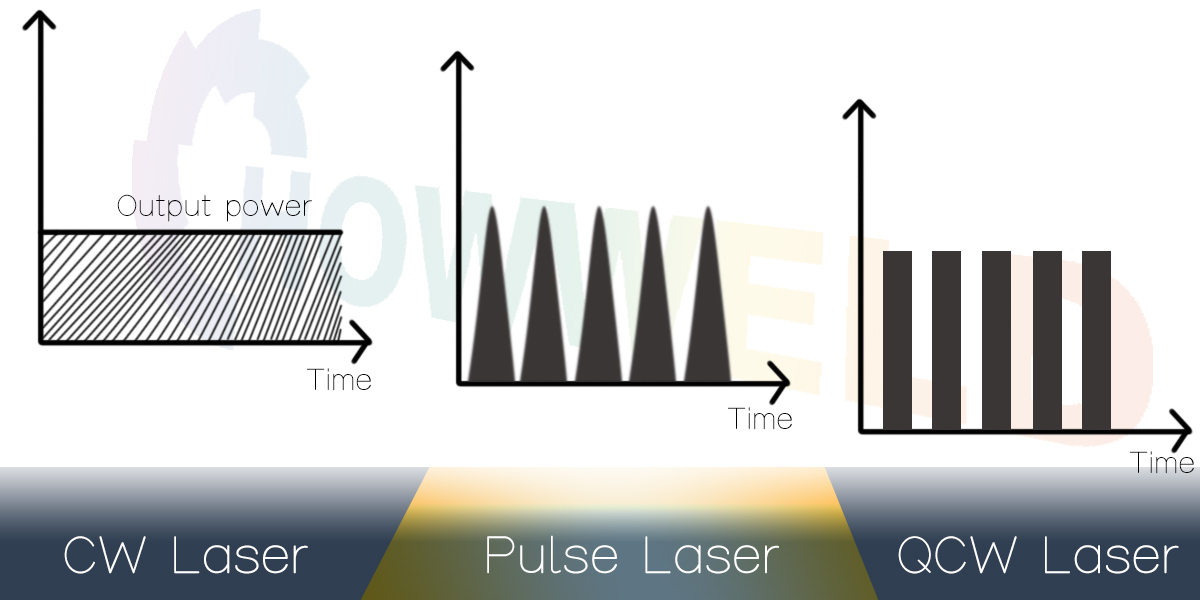
QCW Laser CNC Welding (Quasi-Continuous Wave) is a laser welding technology that combines aspects of both continuous wave (CW) and pulsed laser systems. It delivers high peak power in short bursts or pulses while maintaining the ability to operate in quasi-continuous mode, making it an efficient and versatile option for various industrial applications. Here’s an overview:
1. How QCW Laser Welding Works
Quasi-Continuous Operation: QCW lasers emit a continuous beam with periodic pulses of high energy. These pulses allow the laser to achieve high peak power for short periods, delivering intense bursts of energy to the material.
Pulse Control: The ability to control the pulse duration and energy allows for precise welding and minimizes thermal distortion, especially in delicate materials.
High Peak Power: QCW lasers can generate very high peak power (much higher than CW lasers) during the pulse, making it effective for welding materials that require more energy input to melt and join.
2. Advantages of QCW Laser Welding
High Precision: QCW lasers offer excellent control over the welding process, allowing for fine and detailed welding in applications requiring high accuracy.
Low Heat Input: By delivering energy in pulses, QCW lasers reduce the overall heat input into the material, minimizing thermal distortion, making it suitable for thin materials and delicate components.
Flexible Pulse Duration: The pulse length can be adjusted based on the material, providing flexibility for different welding applications.
Cost Efficiency: QCW lasers can sometimes be a more cost-effective alternative to traditional pulsed lasers since they combine the benefits of both continuous and pulsed modes.
Versatility: QCW lasers can weld a variety of materials, including metals and some non-metal materials. They are particularly effective for welding reflective metals like copper and aluminum.
Temporal shaping: unparalleled flexibility Waveform Control
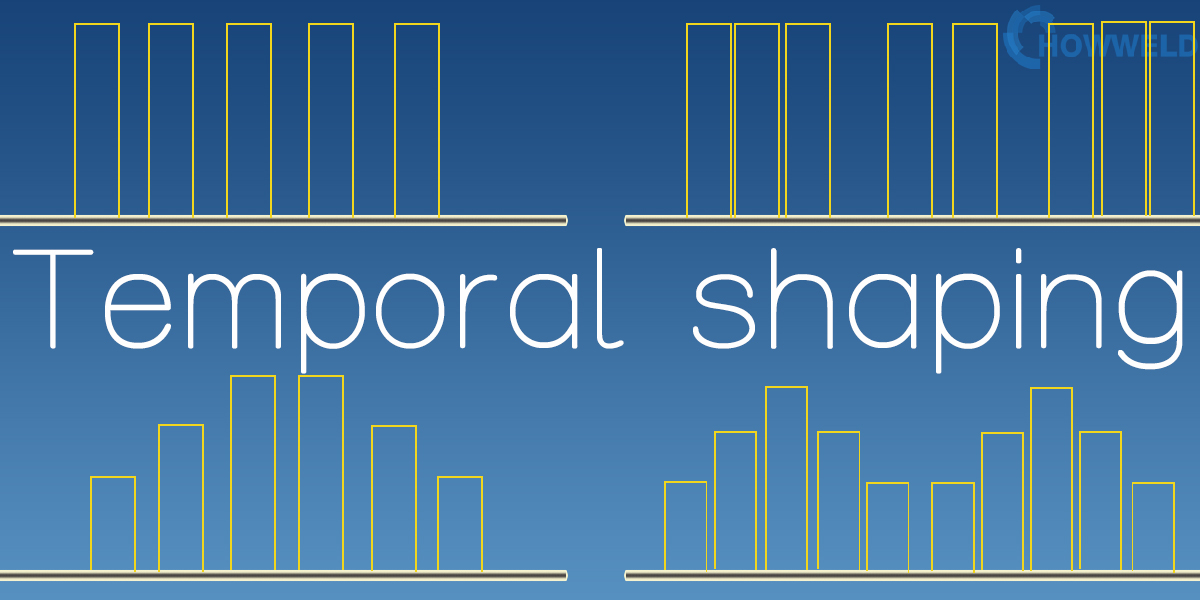
Temporal shaping: unparalleled flexibility Waveform Control
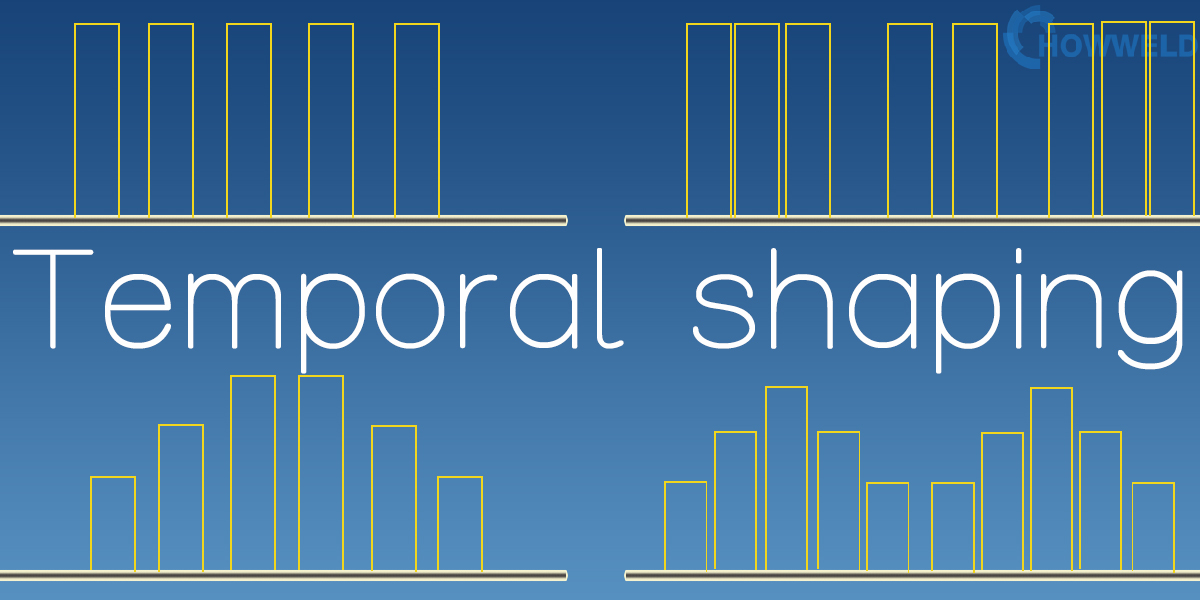
3. Applications of QCW Laser Welding
Medical Devices: QCW lasers are often used to weld small, delicate components like surgical tools, stents, and other medical devices due to their high precision and minimal heat input.
Electronics: Ideal for welding electronic components like sensors, connectors, and micro-circuitry without causing thermal damage.
Jewelry Manufacturing: The precision and minimal distortion make QCW lasers a popular choice for welding fine metals in jewelry production.
Battery Manufacturing: QCW lasers are used in the production of batteries (such as lithium-ion) to weld thin foils and terminals with minimal thermal impact.
Aerospace and Automotive: They are suitable for welding lightweight materials (like aluminum and titanium) used in aerospace and automotive industries.
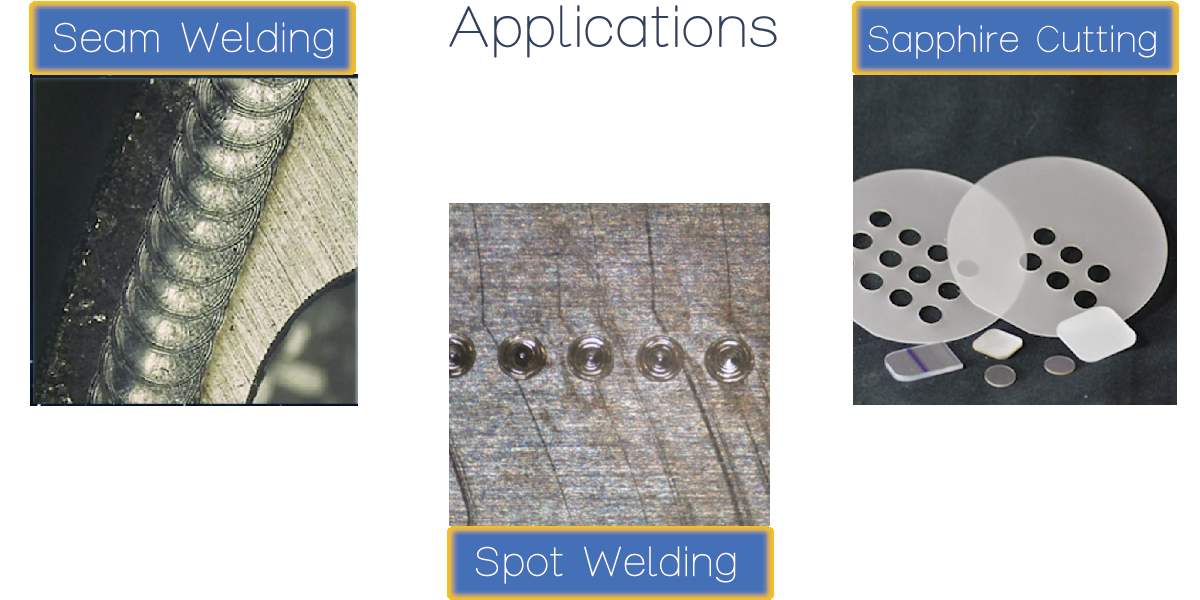
4. Materials Suitable for QCW Laser Welding
Stainless Steel
Copper and Copper Alloys
Aluminum and Aluminum Alloys
Nickel and Nickel Alloys
Titanium
Precious Metals (Gold, Silver)
5. Key Features
High Peak Power: Up to 10 times higher than CW lasers, ideal for cutting and welding high-reflective or thermally conductive metals.
Energy Efficiency: Lower energy consumption compared to pulsed lasers, making it more efficient for industrial-scale production.
Compact and Flexible: QCW lasers are often compact, making them easy to integrate into existing manufacturing systems.
6. Limitations
Limited to Thin Materials: QCW lasers are most effective on thin or delicate materials, and might not be suitable for very thick or heavy-duty materials.
High Initial Cost: QCW laser systems, though cost-effective in operation, may have a higher initial investment cost compared to traditional welding methods.
7. QCW vs CW Laser Welding
QCW: Offers higher peak power with pulsed energy bursts, suitable for precise welding with minimal heat input.
CW: Delivers continuous energy, better for deeper welds and applications requiring steady power input but may cause more thermal distortion.
QCW laser welding is particularly useful when high precision, minimal heat input, and flexibility in energy control are needed, making it ideal for industries like medical devices, electronics, and aerospace.
Laser Welding / Automatic Laser Welding Machine / QCW Fiber Automatic Laser Welding Machine
Quasi Continuous Wave Automatic Fiber Laser Welding Machine