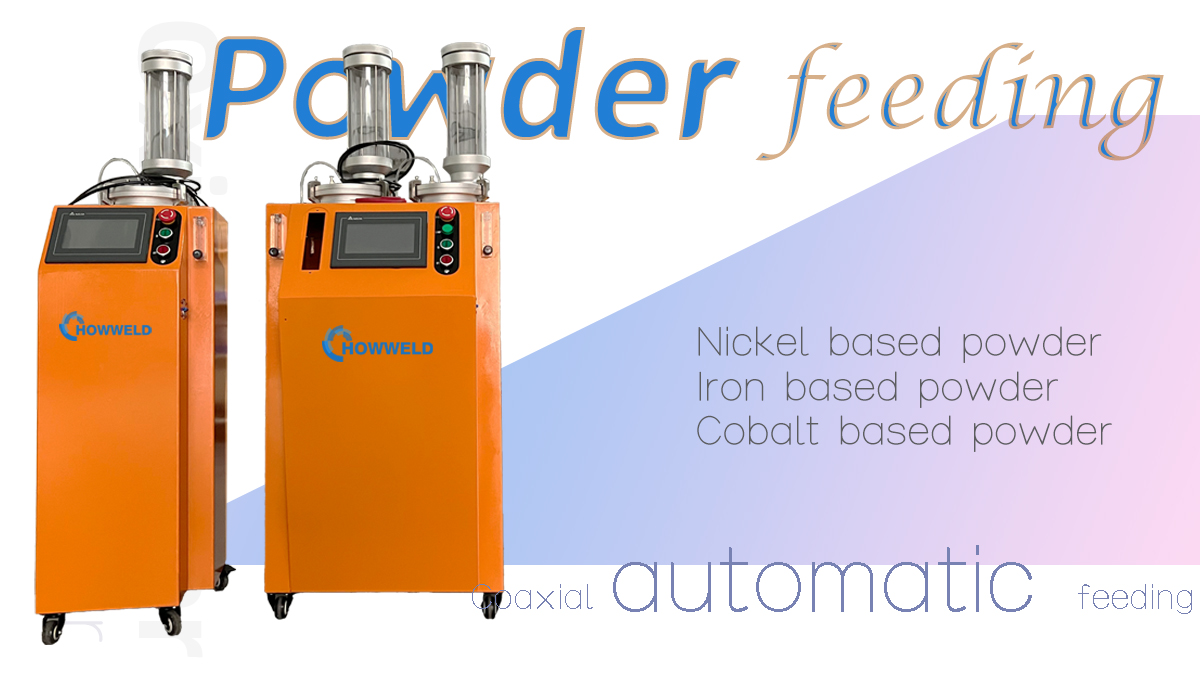
1. The working gas pressure setting range is between 0.4MPa-0.6MPa.
2. Before use, the alloy powder should be baked at 100-150 degrees for 30-40 minutes. After cooling, it can be loaded into the powder feeder, and the powder top cover should be tightened (the powder should be sieved several times before and after baking).
3. Before starting powder feeding, it is necessary to confirm whether the gas passes through to avoid powder blocking. If the powder tray or powder feeding pipe is blocked, the gas flow should be increased. After no blockage, adjust the flow to the specified value according to the actual powder feeding situation.
4. The powder manufacturing process and particle size range will affect the powder feeding accuracy. This powder feeder supports 200
The powder below the mesh, too fine powder is easy to cause powder accumulation.
5. The parameters of the powder feeder have been adjusted before leaving the factory, and the user cannot change or disassemble it at will.
6. When not in use for a long time, remember to empty all the powder in the powder feeder and blow it clean with a dry airflow. The phenomenon of powder retention may be caused by the following reasons:
(1) The gas flow of powder feeding gas is insufficient, please adjust the gas flow to the corresponding speed, and try to find out by yourself.
(2) Insufficient air pressure of gas cylinder or gas source.
(3) The particle size of the powder does not meet the requirements of the equipment, and the powder is too fine.
(4) The powder is mixed with impurities and is not sieved.
(5) The powder is wet and not dried.
7. When opening the rear switchboard door, do not sprinkle or drop powder into the switchboard to avoid damage to electrical components.
Parameter index
Work category |
Single barrel |
Gas type |
Argon |
Flow range |
1-20L/min |
Pressure range |
-0.1-1MPa |
Bucket volume |
1.2L |
Sub disc speed |
0.00-10.00r/min |
Power particle size |
90-300 mesh |
Powder feeding accuracy |
《0.5% |
Supply voltage |
220V |